11月22日,艾邦于深圳机场凯悦酒店举办了第三届动力电池复合集流体大会,共17个专业议题,1个圆桌论坛, 500+参会人员,此次论坛在各位嘉宾、赞助商、与会者以及艾邦工作人员的配合支持下获得圆满成功。
江苏亨通CTO李华清给大家带来了主题报告《复合集流体生产工艺及其技术难点》。下面,小编给大家整理了李总的精彩演讲内容。
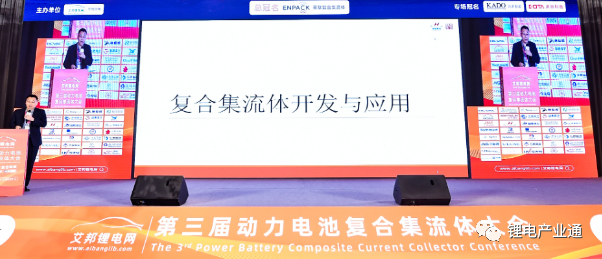
目前的二次电池,正负极材料的导电能力有限,为了提高电池的使用效率,都需要集流体。不需要集流体的电池,也有研究和开发。但尚未进入工业化应用。
从传导性能来说,铜最好,但是铜的价格昂贵,密度比较大,所以铝箔也是很好的选择。但是在正负极这个工作环境中,铝可能会与金属锂发生反应。产生锂枝晶,所以目前我们的电池集流体里用的是铜箔和铝箔两种材料。
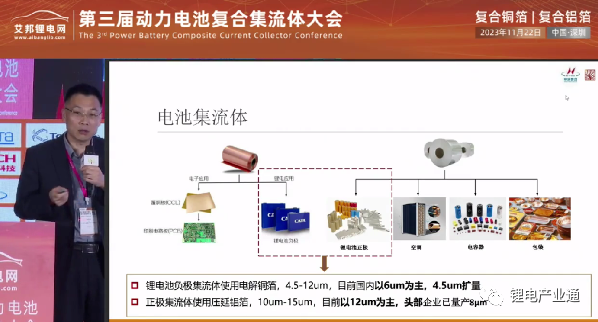
集流体材料的选择,有很多企业做了大量的尝试,他们做集流体,除了铜箔和铝箔以外,有用金属的,有非金属,有铜带、铜合金、不锈钢、铜网,镍带、材料五花八门,大家在提高性能和降低成本方面做了大量的尝试。
复合集流体的工艺,目前复合铜箔和复合铝箔的工艺有些区别,复合铝箔用一台设备就可以搞定,只不过现在随着工艺和装备的不断提升,大家对材料的认识进一步加强,装备上有重大的创新,从以前的几十遍到目前的几遍,有的企业可以镀一遍。
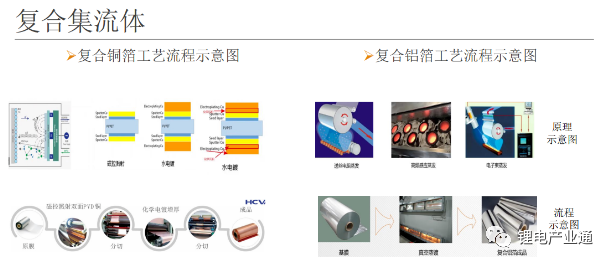
薄膜金属化,是塑料薄膜镀上金属层后可以导电,是一个复合材料,也可以叫层状金属或者层状复合材料,利用了高分子和金属叠加的优势。
清华大学何老师在2013 年的文章提到了金属化薄膜在电池领域可能会得到应用,10 年之后,这个材料从实验室里搬到了中试线上,现在已经进入到规模投资的阶段。
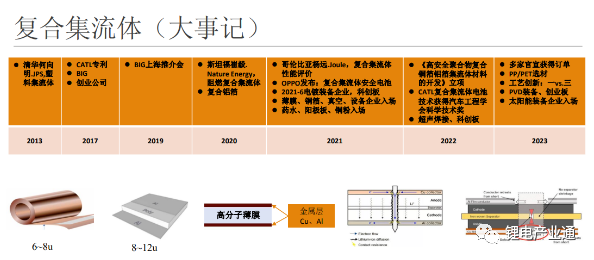
2017 年,国外创业机构soteria,成立了BIG联盟,中国以宁德时代为代表的电池企业,分别启动了复合集流体的产业化。专利布局都是在 2017 年大规模出现,从这个阶段布局已经启动,到目前为止,专利的数量其实还不大。
目前 PET和 PP这两种材料作为基膜,在我们复合集中体上有一个选项,因为正负极材料电压不一样,所以正负极的工况还是有区别的。
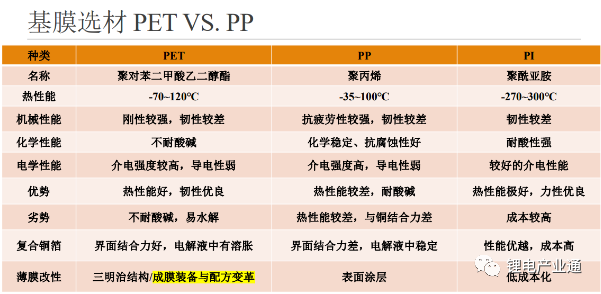
对于复合铝大家没有提出质疑,认为PET就 OK 了,但是用作负极的复合铜箔,希望提高它在电解液中的耐腐蚀能力,在电解液环境当中,PP的耐腐蚀能力优于PET。
PET是聚酯薄膜分子链相对复杂,所以薄膜表面的结合跟第二层结合强度更高。那么 PP 的分子链比较干净,没有那么多支链,薄膜表面的达因值就相对较低,这种薄膜在电解液环境中,耐酸碱能力更强,但是与金属层界面结合力不如PET。
目前在PET和PP的改性方面有很多企业也在考虑,特别是做薄膜的行业,也提出了三明治结构的薄膜,PET不耐腐蚀,那就把PET包在中间,两边用PP,但是PP的结合力不好,就把 PP放在中间,两面做涂层。
我们对复合铜箔和复合铝箔进行一个梳理,这是两步法、三步法的示意图。
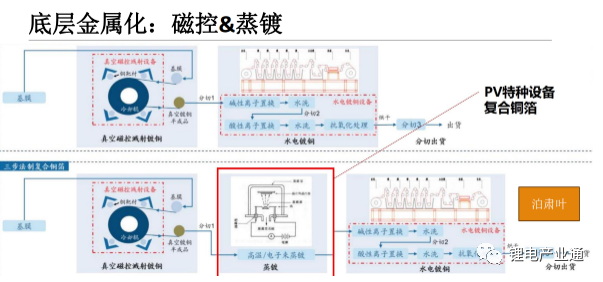
沈阳的泊肃叶提出一种工艺,以蒸镀的方式把PET磁控溅射的基膜进一步加厚。这样有两个好处,首先,增厚的种子层,它的致密性是增加的。第二由于导电层增加,后续电镀过程中,它的速度就会提升,那么整个产线的利用率就会进一步加强,生产效率就会提高,那么设备数量可能会降低,这对大家投资的回报能够产生重大的影响。
所以,对于两步法和三步法,大家应该以科学的态度来对待。最初可能由于我们路线的选择,造成了必须用装备来满足我们的工艺,但是经过探索以后发现,还是各有优势的,所以在各位企业家选择的时候,这个因素还是要慎重考虑。
我们目前普遍采用的两步法,需要电镀,现在电镀加厚行业里,以东威科技为代表的,是采用了双边夹的方式,那为什么要这么做?
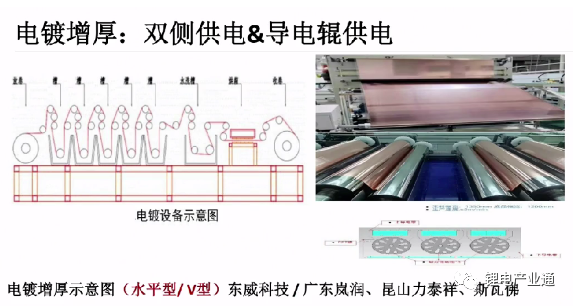
因为在 2017 年最早开始做这个尝试,从实验室进入到中式产业化的过程中,发现 v 型辊设备,成品长度不能保证。东威科技采用双边夹的方式充电,解决了这个问题,但是它也有局限,幅面宽度要定尺,对于溅射质量要求高,生产过程的电流密度,均匀性都受到一定限制。
现在也有企业在攻关,用导电辊的方法,例如,广东岚润,昆山力泰祥、斯瓦佛,昆山元天电子等,他们做的一些尝试就是在导电辊上导电,其中有 v 型、 c 型的,方式很多。
我们说到磁控溅射设备,现在捷佳伟创推出了一个新型的理念,把基膜腔和收放卷,隔离开来,每一个腔体的靶材数量是可控的,不至于因为靶材过多,导致生产过程失控。
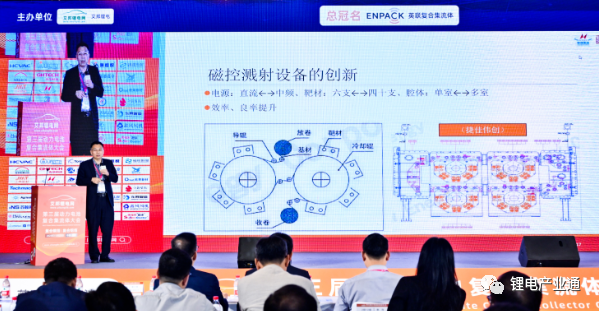
同时因为是一个独立的真空腔,可以做多腔体,靶材目前可以做到 40 支,这样的构型,首先因为打开多了,它的速度可以大幅度提升。第二,这两个腔体是分离的,腔体与腔体之间有截止阀来保真空,所以在生产过程中,它不需要完全脱身来取膜了,它的生产效率有可能会进一步提升。
在生产过程当中存在一系列的问题,除了力学性能表面的结合力以外,还有透光,针孔,致密性等。有研究尝试用打孔铜箔、铜网来做集流体,只要能打通就行,但是毕竟它是一个微米的厚度,所以致密性,将来对电池的使用效率,特别是在快充快放过程中的发热还是有影响的。
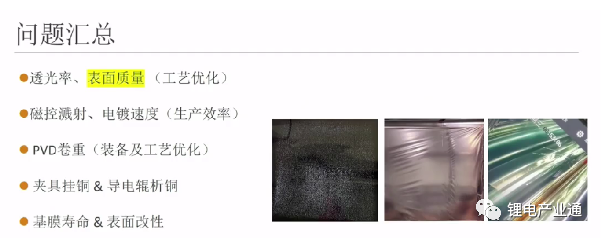
现在电解铜箔的生产线比较短,而复合集流体是先通过磁控镀膜,下线后再进入电镀,电镀线目前一般在 40 米左右,这么长的距离,这么薄的薄膜,对整个系统的控制要求非常严格,所以对这种薄膜的表面质量要求是非常高的。
目前,这个横向、纵向的纹路,皱褶,这些问题都需要靠我们的装备和工艺来设计解决。
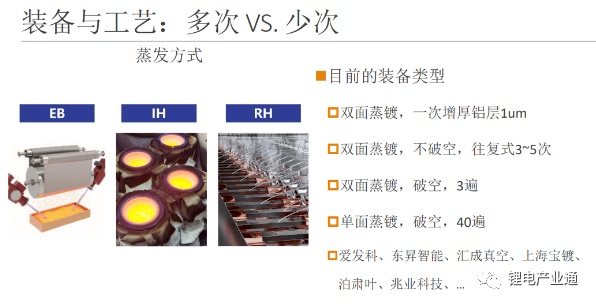
有些是单面的,单面蒸镀一层,掉头,再来蒸镀第二层,每一次要开仓,要破真空。这种传统的方式用在头部企业的装备上,需要40 遍,因为蒸镀按照传统的设备来做这个工作,每一次是在几十个纳米范围内,单侧要达到1微米大概要 20 遍左右,这样的话总共就是 40 遍。这就有一个问题,每一遍头尾有废料,每一次破真空表面有氧化层,那么方阻就会受影响。
就是单次和多次的的导电,包括拉伸以后的电解会有变化,对使用过程是有影响的。我们拿到静态数值和动态数值的数据,如果大家只看静态数值,会对你产生误导。
现在有的企业也推出了新的设备。像爱发科,东昇智能,汇成真空、宝镀、泊肃叶、兆业科技等,他们都有类似的装备和工艺技术。
那么大家的区别是什么呢?有一遍搞定的,有两到三遍的。如果是一遍成膜,那性能就会非常的好。但是,散热问题要解决。目前的卷重有限,跑到 3 千米就跑不动,再跑热量就跑不出来,这是一个大问题。但是创新不断,上海宝镀在做全新的尝试。
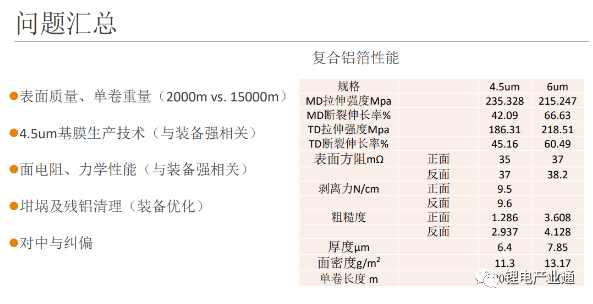
所以这个产品装备的升级和改革,到目前为止来看,还有很大的空间,大家可以去做。右侧是一组数据,目前 4.5 微米的基膜,做双面镀铝的难度非常大。
现在看这个数据,4.5微米的方阻只有 35mΩ ,这个性能是很 OK 的。如果基膜选择的合适,可达到 200 Mpa以上,这个产品如果使用起来,只能是电池厂动手换掉。现在除了减重以外,还希望减薄。
如果 以4.5 微米的评估,目前压延铝箔主力的厚度是 12um,减薄的效果明显,因为汽车底盘就那么点空间,减薄都是以毫米来计算,如果我们 1000 平方米的集流体,经过缠绕以后,对汽车空间的增加,意义还是挺大的。
这是一个一体化的设计概念,它的概念是什么呢?薄膜生产出来以后,现场就把它做成低酯化薄膜。其实有几个企业在做,包括英联,双星等。
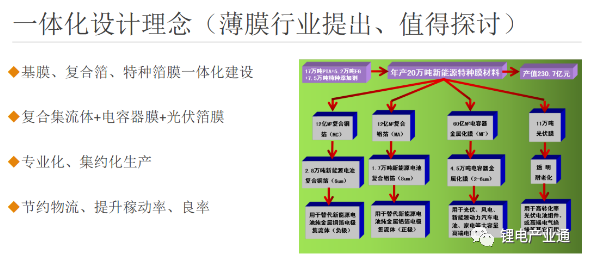
如果这个薄膜以复合集流体为主打,同时能生产这个电容器的薄膜和光伏的光膜,这样它的副业可以支撑它正常的运行,一旦复合集流体正常打开,就把产能补起来。
首先是真空设备,就是双面、连续化、快速、高品质,这是大家应该追求的,现在原型机都出来了,但是你要想做到量产化,降低自己的成本、单位面积成本,这些问题是要考虑的。
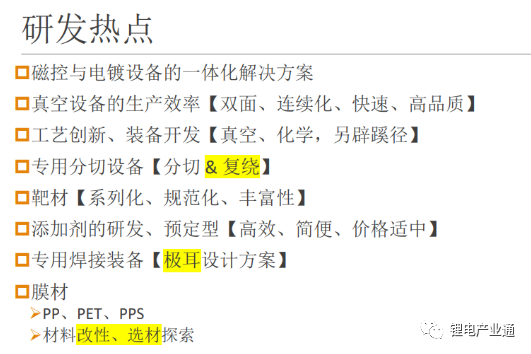
接下来是工艺的创新,装备开发,工艺上还要配套才能用得好,辅助的材料也要跟得上。
专用的焊接装备,涉及到极耳的设计问题,即便是极耳焊上以后,导入和导出也是造成热量增加的主要原因。比如高速上越多车道,下高速的时候会更堵,因为接口是窄的,极耳也类似。复合集流体的极耳焊接工艺和装备,目前有专业机构和企业做了大量的创新。装备和工艺已经应用在中试线上。
还有就是关于材料的改性、选材问题。
目前整个资本市场对我们这个行业寄予厚望,投资热度过高。刚才主持人介绍全行业投资意向100 亿平米的量,大家可以去对应一下,1个GWH对应 1000 万平米,那么这 100 亿平米就对应1000个GWH,1TWH对应 1000 万辆电动汽车。
马斯克表示,未来十年有 240 TWh的储能容量,有巨大的产能空间。
在 2023 的世界动力电池大会上,宁德时代的董事长提出,2030年动力电池的需求是 4800GWh,储能是1000GWh,这是给大家的打气。
4.8TWh,意味着2023年出货约1000GWh,今后7年,电动汽车连续年均增长率超过25%。今年我们看到的市场没这么乐观。但储能的发展空间巨大,同样值得大家期待。
新能源汽车的快速发展带动了动力电池的高速增长。动力电池生产流程一般可以分为前段、中段和后段三个部分。其中,前段工序包括配料、搅拌、涂布、辊压、分切等,中段工序包括卷绕/叠片、封装、烘干、注液、封口、清洗等,后段主要为化成、分容、PACK等。材料方面主要有正负极材料,隔膜,电解液,集流体,电池包相关的结构胶,缓存,阻燃,隔热,外壳结构材料等材料。
为了更好促进行业人士交流,艾邦搭建有锂电池产业链上下游交流平台,覆盖全产业链,从主机厂,到电池包厂商,正负极材料,隔膜,铝塑膜等企业以及各个工艺过程中的设备厂商,欢迎申请加入。
长按识别二维码关注公众号,点击下方菜单栏左侧“微信群”,申请加入群聊