汽车电动化表现为新能源车的渗透率逐步提升,汽车核心部件从内燃机变为三电系统。新能源车替代传统燃油车已经成为不可逆转的趋势。技术竞争变为围绕三电的技术研发和资源争夺。
汽车要完成智能化升级,一方面,需要增加智能座舱和自动驾驶等智能化模块;另一方面,智能化要求汽车整车架构从传统的机械式向更智能的电子电气架构转化(Electrical and Electronic Architecture,简称 EEA)才能支撑智能化对于运动控制的要求。
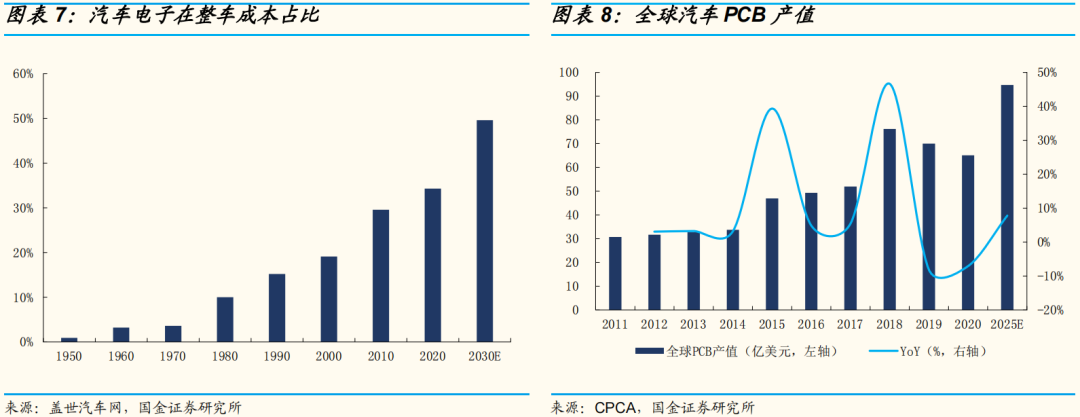
汽车的电动化和智能化的底层硬件支撑就是汽车电子模块,电子化使得汽车电子成本占比不断提升,预计到2030年汽车电子成本占比将接近50%,而PCB作为电子之母,其在汽车上的应用也将明显提升,根据CPCA预计,2025年全球汽车PCB产值将达到95亿美元,2020~2025年的复合增速将达到7.8%。
汽车类PCB以4-8层板为主,产品可靠性及稳定性要求高,价格稳定、波动小,产品认证周期长。
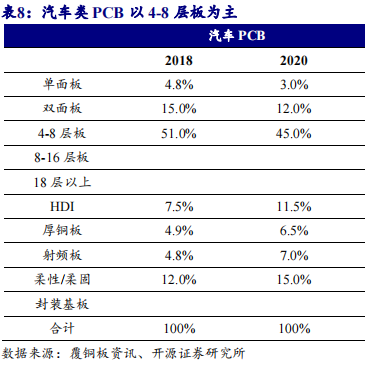
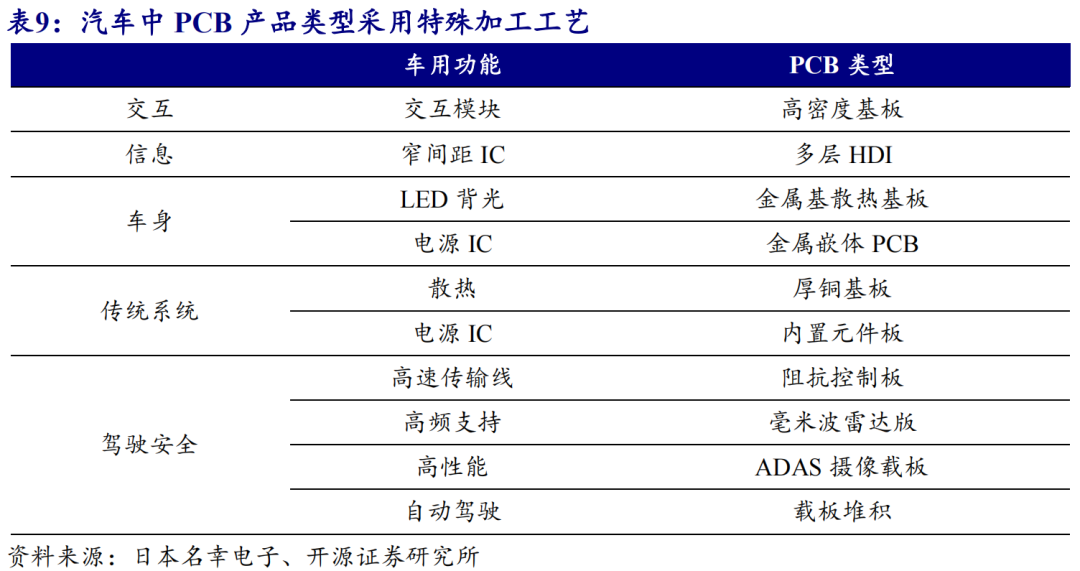
800V 高压快充将成为主流方案。电动车充电功电压提高后,元器件的尺寸会变大,相应的PCB走线需要承受更大的电流。在设计时需要避免发生过载、过热或充电电流受控降额等问题,此时多会使用厚铜或嵌入铜方案:厚铜PCB高多层化,引入埋铜、嵌铜工艺增加散热能力。
汽车BMS系统的轻量化需求
在动力电池BMS管理的电池模组,用FPC替代线束,从而达到轻量化的要求和节省空间的目的。
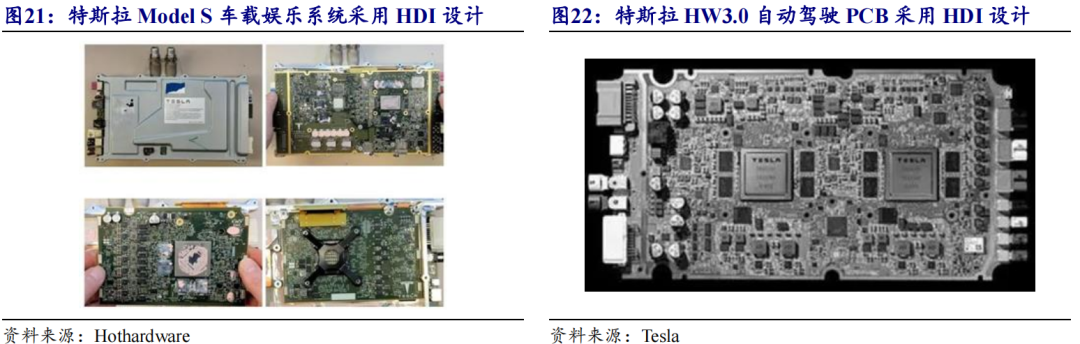
图片来自:Amphenol
高阶感知系统离不开软硬结合板
高阶自动驾驶系统由感知层、决策层、执行层三部分构成。感知层由摄像头 CIS和雷达收发器构成,决策层由摄像头ISP和信号处理器构成,执行层由各个执行模块构成。
由于对于可靠性要求更高,摄像头、激光雷达等传感器会优先使用软硬结合板的互连方案而放弃使用连接器。
智能座舱需要高多层 HDI PCB
车内智能座舱将多个不同操作系统和安全级别的功能融合,满足触控/智能语音/视觉识别/智能显示等多模态人机交互,AR-HUD、电子外后视镜等方案涌现。高度集成、超强运算性能,推动HDI用量增加。车载娱乐系统、自动驾驶主控、车载服务器等核心环节的PCB通常采用高速材料,10层以上3阶HDI设计。
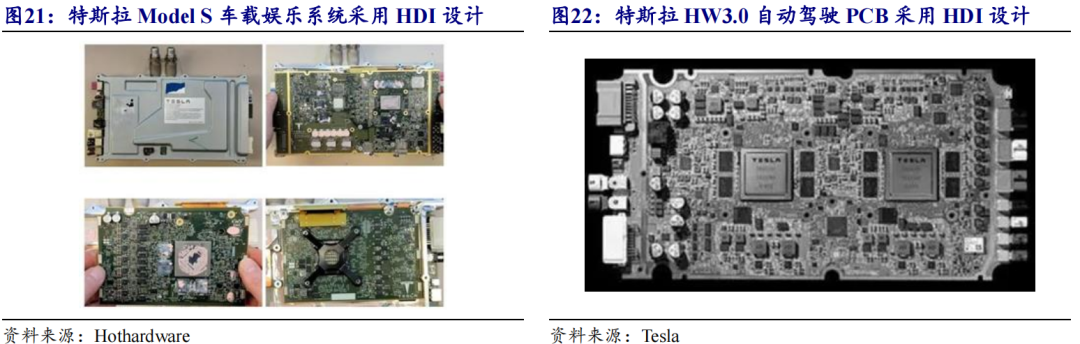
三电+域控是价值核心,大陆 PCB 迎变革机会国金证券[樊志远,邓小路,刘妍雪]