硅碳负极技术路线
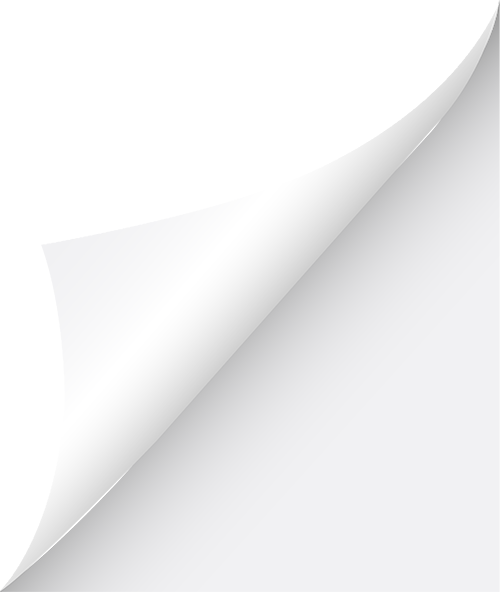
目前可产业化的硅基负极技术主要分为二类,分别是硅氧和硅碳。
硅氧负极主要分为三种路线:硅氧(氧化亚硅);预镁硅氧;预锂硅氧。
硅碳负极主要分两种技术路线:砂磨纳米硅与石墨混合;CVD法将纳米硅沉积到多孔碳。
采用氧化亚硅与石墨材料复合。氧化亚硅的结构中存在一定的氧原子,这使得其在嵌锂过程中的体积膨胀相比纯硅材料大大减小,循环性能得到较大提升。其优点是循环性能和倍率性能较好,率先在动力电池领域得到应用。缺点是首效较低,需要通过预镁或预锂工艺提升首效,且制备工艺较为复杂,成本较高。
硅氧常用量产制备工艺:Si+SiO2→高温炉热处理→冷凝→氧化亚硅(SiOx)前躯体→粗碎→粉碎→CVD炉炭包覆→第1代硅氧。相较单质硅颗粒,氧化亚硅(SiOx)在锂嵌入过程中发生的体积膨胀较小,因此相对纯硅负极,其循环稳定性有较为明显改善,但是氧化亚硅在充放电过程中会生产Li2O等非活性物质,导致SiOx材料首次效率较低(约70%)。

预镁硅氧常用量产制备工艺:Si+SiO2+Mg→高温炉热处理→冷凝→预镁的氧化亚硅(SiOx)前躯体→粗碎→粉碎→CVD炉炭包覆→第2代预镁硅氧。通过预镁阻止SEI膜合成可将首效提升到80%左右。但综合来看,由于预镁化产品普遍克容量不高,预镁工艺会增加10-20万/吨的材料成本,但首效仅提升到82%-83%左右,对于电芯厂来说性价比较低。同时由于镁热反应产热较大,预镁材料晶粒变化相对较大,不利于材料循环性能。
预锂硅氧常见量产制备工艺:Si+SiO2→高温炉真空热处理→冷凝→氧化亚硅(SiOx)前躯体→粗碎→粉碎→CVD炉炭包覆→第1代硅氧→添加锂粉或锂的氧化物混合→烧结→ 第3代预锂硅氧。在第2代预镁硅氧基础上进一步提升了首效(ICE提升至86%-92%),但是目前能够兼顾安全稳定、成本较低、可大规模生产的预锂化技术还不够成熟。
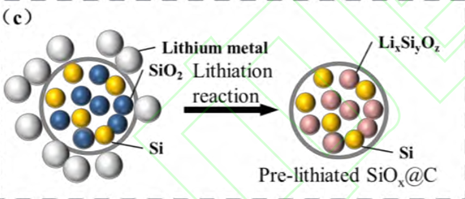
将硅与石墨材料混合,硅作为活性物质提供高容量,碳材料作为载体缓冲硅在充放电过程中的体积膨胀,同时提高负极材料的导电性能。碳材料的包覆能在其表面形成 SEI 膜,抑制电解液对负极的侵蚀,从而提高循环性能。硅的引入使得硅碳负极具有较高的克容量,相比传统石墨负极,其能量密度有显著提升。并且其制备工艺中碳材料复合和烧结等步骤技术较为成熟。但硅在脱嵌锂离子时体积膨胀较大,这会导致硅颗粒分化及 SEI 膜的破裂增厚,影响电池的首充效率与寿命。
硅碳常用的量产制备工艺:工艺硅→三氯氢硅→块状硅→砂磨法→纳米硅粉→与石墨复合→第1代砂磨纳米硅炭负极。研磨法主要的问题就是粒径较大,且容易引入杂质,纯度较低,且粒径分布不能有效控制。
气相沉积硅碳技术路线:硅源→热分解→无定型纳米硅+多孔碳骨架→气相沉积硅碳→CVD炉碳包覆。核心是通过低成本生产一种多孔碳骨架来储硅,并通过多孔碳内部的空隙来缓冲硅嵌锂过程中的体积膨胀,因此膨胀率低,循环优异。同时由于生产流程短,设备少,理论成本低,被认为是最有前景及性价比最优的批量应用硅负极解决方案。
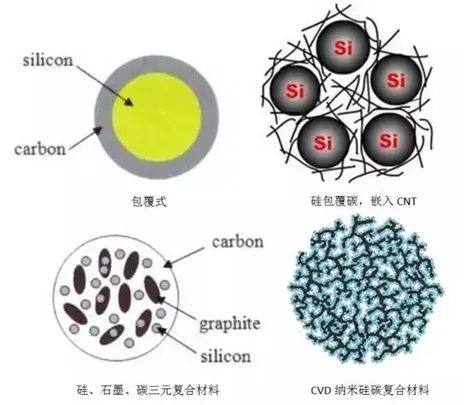
原文始发于微信公众号(埃普诺集团):硅碳负极技术路线
新能源汽车的快速发展带动了动力电池的高速增长。动力电池生产流程一般可以分为前段、中段和后段三个部分。其中,前段工序包括配料、搅拌、涂布、辊压、分切等,中段工序包括卷绕/叠片、封装、烘干、注液、封口、清洗等,后段主要为化成、分容、PACK等。材料方面主要有正负极材料,隔膜,电解液,集流体,电池包相关的结构胶,缓存,阻燃,隔热,外壳结构材料等材料。 为了更好促进行业人士交流,艾邦搭建有锂电池产业链上下游交流平台,覆盖全产业链,从主机厂,到电池包厂商,正负极材料,隔膜,铝塑膜等企业以及各个工艺过程中的设备厂商,欢迎申请加入。
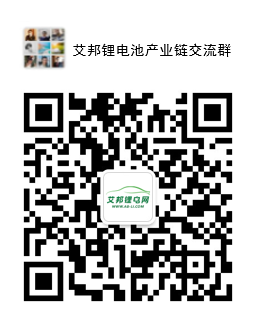
长按识别二维码关注公众号,点击下方菜单栏左侧“微信群”,申请加入群聊