一、干法电极介绍:较传统湿法是工艺的全面升级,更适配新一代电池需求
(一)极片生产环节决定电芯的基本性能
极片生产是电芯制作的前段环节,对电芯的基本性能起决定性影响,而干法工艺是新的 极片生产方式。极片生产是电芯制造的首要环节,主要分为浆料搅拌、极片涂布、极片 辊压、极片分切四个步骤。极片生产占设备、人工、厂房成本的 35.75%,能源成本的 57.23%, 是电芯制造步骤中成本最高的环节。 浆料搅拌:将正/负极活性物质、导电剂、粘接剂按比例均匀分散在溶剂中并搅拌, 形成具有一定粘度的稳定浆料,该工序占设备、人工、厂房成本的 7.91%。 涂布干燥+溶剂回收:传统的湿法涂布是将搅拌均匀的浆料涂覆铜/铝金属箔集流体 上,并将复合物送进干燥箱中蒸发溶剂,对溶剂进行回收。两个工序占设备、人工、 厂房成本的 19.56%,能源成本的 48.20%。 辊压:将涂布后的极卷置于辊压机的双辊下,通过挤压极片实现理想的厚度及界面 一致性。该工序占设备、人工、厂房成本的 5.19%。 分切:将经辊压后的宽极片纵切成窄极片,断面的毛刺大小及形貌特征会直接影响 卷绕或叠片的质量。该工序约占占设备、人工、厂房成本的 3.09%。
(二)干法与湿法的工艺介绍及材料对比
传统湿法工艺是将活性物、导电剂、粘接剂按比例混合在溶剂中,并通过狭缝涂布模头 按要求涂覆在集流体表面并辊压。 干法工艺是将活性颗粒、导电剂和进行干混均匀后加入粘接剂,在粘接剂原纤化作用下 形成自支撑膜,最后辊压覆盖在集流体表面。
(三)干法制膜工艺介绍
1、自支撑膜制备工艺
干法制膜包括:粘接剂原纤化法和静电喷涂法,其中粘接剂原纤化是主流。静电喷涂法 在后续的可加工性、粘连稳固性、电极柔韧和耐久上表现不如粘接剂原纤化法。2019 年 特斯拉收购 Maxwell 公司,Maxwell 主要采用粘接剂原纤化制膜,而特斯拉目前也是采 用粘接剂原纤化法制造自支撑膜。 粘接剂原纤化法是将活性物质粉末与导电剂混合后加入 PTFE 粘接剂,然后对干混 合物施加外部的高剪切力,使 PTFE 原纤化后粘合电极膜粉末,最终挤压混合物形 成自支撑膜。 静电喷涂法是用高压气体预混活性物质、导电剂以及粘接剂颗粒,在静电喷枪的作 用下使粉末带负电荷并喷至带有正电荷的金属箔集流体上,然后对载有粘接剂的集 流体进行热压,粘接剂融化后会粘连其他粉末并被挤压成自支撑膜。
Maxwell 在粘接剂原纤化方案上具有专利的领先优势。美国和日本分别是粘接剂原纤化 法和静电喷涂法工艺的领先国家,其中,Maxwell 和 Toyota 各是两种工艺的代表公司。 截至 2022 年 5 月,Maxwell 在粘接剂原纤化方案上的专利数量 37 个,专利数量排名第 一,公司在此工艺上的成熟度具备领先优势。
2、干法工艺原纤化技术原理
原纤化是在外部剪切力的作用下,PTFE 变成原纤维的过程。由于 PTFE 范德华力较低, 堆积松散,在外部剪切力的作用下会从团聚物变成原纤维,原纤维呈网状粘合电极粉末。 温度、剪切是影响 PTFE 原纤化的重要因素。当温度高于 19 度,PTFE 会从三斜晶 系转变为六方晶系,分子链会变软,也是形成原纤维的主要原因。
原纤化制膜是极片辊压的前段环节,主流的原纤化制膜机器为:1)气流粉碎机;2)螺 杆挤出机;3)开炼机。在 PTFE 与活性物质充分混合后,混合物被送入原纤化制膜机, 在机器的辊压下混合物会形成自支撑膜。Maxwell 实验数据显示,进料速度越小,原纤 化电极膜的阻抗越大;与此同时,电极膜阻抗会伴随辊压的力度增加而降低。
(四)干法 VS 湿法:优劣对比
1、干法工艺成本更低,制造成本降低 18%
干法制造工艺步骤更少,电芯制造成本综合降低 18%,降幅 0.056 元/Wh1。传统湿法工 艺中,涂布干燥及溶剂回收环节,分别占设备、人工、厂房成本和能源成本的 22.76%和 53.99%。干法工艺将传统湿法的浆料涂布改为制造自支撑膜,因此它无需 NMP 溶剂, 省去了电极干燥及溶剂回收环节,实现更低的电芯制造成本。
干法工艺对环境更友好,且更适配大规模生产。NMP(N-甲基吡咯烷酮)溶剂有毒,对 环境不友好,且在传统湿法工艺中需要对其进行回收,会消耗大量的能量。干法工艺无 需溶剂,在极片涂布环节减少烘烤及溶剂回收环节,工艺流程更简单,设备占地面积更 小,更适配极片的大规模生产。
2、干法工艺提升活性物质压密,能量密度提升 20%
干法电极在 PTFE 原纤化的作用下,较湿法电极可以实现更加平整的形貌。由于湿法需 要溶剂,在溶剂蒸发后,活性物质与导电剂之间会留出更多空隙,空隙导致材料的压实 密度不高。干法不存在烘干过程,因此不存在溶剂蒸发后留下的空隙,颗粒之间的接触 更为紧密。
干法电极可以做到更大的压实密度。干法条件下压实后,裂纹、微孔等问题更少。磷酸 铁锂压实密度可从 2.30 g/cm3 提升至 3.05 g/cm3,提升幅度 32.61%;三元材料压实密度 可从 3.34 g/cm3 提升至 3.62 g/cm3,提升幅度 8.38%。石墨负极压实密度可从 1.63 g/cm3 提升至 1.81 g/com3,提升幅度 11.04%。由于单位体积下含有更多的活性物质,因此干法 电极也具备实现更大能量密度的技术路径。相同条件下,干法电池能量密度可提升 20%。根据 Maxwell 的实验数据,干法电极 能量密度可以超过 300 Wh/kg,且具备实现 500 Wh/kg 的可能性。 干法电极厚度极限更大,可以提升面容量。传统湿法电极涂布厚度极限是 160 µm, 而干法的厚度区间为 30 µm-5 mm。更大的厚度区间也能适配更多样的活性物质。
3、干法电池电性能更优
干法工艺电池的循环性能、耐久度和阻抗在实验室条件下均更优。由于目前还没有工业 实际生产数据,故本文引用的是《锂离子电池用无溶剂干法电极的制备及其性能研究》 的论文公开数据。
纤维网提升干电极的材料稳定性,进而增强电性能。湿法工艺中,在电池经历 500 圈循 环后,活性颗粒内应力不断积累,导致剖面出现裂纹,最终降低了电池性能。在干法工 艺下,纤维网包覆在活性材料表面,在经历 500 圈的充放电后,网状结构保持完整,颗 粒表面的裂缝较少,与此同时,原纤化后的网状结构能抑制活性物质体积膨胀,防止颗 粒从集流体上脱落,增强了稳定性,提高了电性能。
(五)干电极与下一代电池更适配:固态、预锂化,大圆柱电池
1、固态电池&干电极:抛弃传统液态原材料,但均面临固固界面问题
固态电池是下一代锂电池,抛弃传统液态电解液。从电解质的分类上,固态电池可分为 氧化物固态电解质、硫化物固态电解质以及聚合物固态电解质。氧化物电解质是目前国 内企业布局最多的方向。相比于传统液态电池,固态电池能量密度更高,安全性能更好,
干法电极抛弃传统液态溶剂,与固态电池设计理念类似。在干法技术的赋能下,固态电 池的极片制造过程可以实现完全干燥,消除了湿法工艺烘干后,溶剂分子的残留问题。 此外,利用粘接剂的原纤化作用制造固体电解质膜,能提升固态电池性能,其优势如下:成膜无溶剂,提高离子导电率 ; 固态电解质和粘接剂干混成膜,无需烘干制造成本更低;工艺简单,更适配规模化量产。
2、预锂化&干电极:不用考虑预锂材料与溶剂的兼容性,降低预锂化难度
预锂化策略用于缓解电池首周循环的锂离子损失。锂离子会与负极反应形成 SEI 膜,造 成 6%-15%的锂离子不可逆损失。主流的预锂化策略为负极预锂化和正极预锂化,以正 极预锂策略为例,添加预锂添加剂后,正极锂含量显著增多,有效的弥补了首周充放电 过程带来的锂离子损失。
预锂策略更偏好干燥的电极生产环境。湿法下,溶剂会与预锂添加剂产生副反应,消耗 活性锂,增加电池阻抗削弱预锂效果,干法无需溶剂,干燥的生产环境更适配预锂化策 略的需求。
3、特斯拉 4680&干电极:干电极初次应用于 4680 电池
4680 综合性能优异,具备与麒麟、刀片电池争锋的实力。4680 采用全极耳的设计,以集 流体尾部作为极耳,制作成集流盘的结构,电池容量较 2170 提升 5 倍,能量密度、快充 性能、散热性能等各方面得以兼顾。
4680 实验室样件仅在负极采用干法,正极采用湿法。原因是,在正极辊压过程中,正极 材料容易发生化学变化,正极自支撑膜在辊压后仍容易掉粉。由于干法工艺还未完全成 熟,量产的 4680 电池正、负仍采用湿法工艺。
(六)干法电极技术难点及综合对比
当前国内干电极技术还未完全成熟,仍存在不少工艺技术难点,但干电极本身能给电池 带来性能上的巨大提升,仍然是极具潜力的工艺迭代方向。
干电极工艺较传统湿法是全面的升级。在制造流程上,干电极步骤更少,制造成本及能 耗更低,原料对环境友好,更适配大规模生产;在电池性能上,干法电池可以实现更高 的能量密度,电池的电性能和机械性能均更优;在应用端,干法电池更适配固态电池、 4680 等新一代电池的制造需求。
二、干电极所需新型粘接剂 PTFE,市场空间巨大
(一)聚四氟乙烯(PTFE):干法最佳的粘接剂选择
传统 PVDF 不适配干电极工艺。常用的原纤化粘接剂包括 PTFE、ETEF 以及 FEP,PVDF 不可进行原纤化,但仍可以利用静电喷枪将 PVDF 和其他活性颗粒喷到集流体上,对混 合物热处理后进行压延制膜。但是粘连效果不佳,PVDF 的粘附强度不到 FEP 的 1/4。其 原因是 PVDF 较活性颗粒的粒径太大,削弱了粘连效果,且会降低电极膜的稳定性。 PTFE 是最优粘接剂选择。原因如下:1)聚合分子量较大,可形成更长的原纤维;2) 惰性强且抗腐蚀;3)机械性能良好。但目前国内电池级 PTFE 占比较少,量产仍需 2-5年。
(二)聚四氟乙烯(PTFE):生产工艺介绍
聚四氟乙烯由 TFE 聚合而成,主流的方法包括悬浮聚合法和分散聚合法。在聚四氟乙烯 的生产流程中,上游是萤石矿,酸级萤石矿与硫酸(浓度 98%)在加热炉混合生成氢氟 酸。氢氟酸可以用于制备一系列的氟单体,而其中 HCFC-22 经热裂解可以生成四氟乙烯 (TFE),TFE 可以通过悬浮聚合法或分散聚合法生成聚四氟乙烯(PTFE)。
PTFE 可分为悬浮 PTFE 树脂(占比 50%-60%),分散 PTFE 树脂(占比 20%-35%)以及 分散 PTFE 乳液(占比 5%-30%)三类。分散树脂和悬浮树脂最大的区别在于分散树脂能 实现原纤化,在外部剪切力的作用下能形成丝网结构的纤维。
(三)PTFE:无法直接应用于干电极,必须经过改性
1、钝化粒子表面
PTFE 会与负极表面的锂离子反应生成氟化锂,削弱粘合效果,降低容量。单克 PTFE 大约会消耗 1070 mAh 的锂,电池中的 PTFE 含量越高,消耗的锂也越多。在实验中,排 除首周充放电形成SEI膜的影响后,在第二次放电曲线中,PTFE含量越高放电电流越小, 因此证实聚四氟乙烯会与锂离子反应,影响电池的性能。
在 PTFE 表面涂覆导电碳实现粘接剂的钝化。根据特斯拉的专利介绍,涂层材料包含电 导体(导电碳、炭黑等)以及颗粒材料(粉末状碳材料)。涂层覆盖面积占 PTFE 粒子 表面的 90%以上,厚度介于 0.1-100μm。
2、混合非原纤化材料
原纤化后形成的自支撑膜仍会存在活性物质和粘接剂的粘连作用降低的问题,而活性物 质的脱落会导致电池内部的电阻增加从而影响电池性能。
将 PTFE 与非原纤化材料混合提高电极膜性能。可对传统的非原纤化材料(如 PVDF、 CMC)研磨成为更小粒径的材料,再与 PTFE 混合形成新型的粘接剂。特斯拉专利中混 合物 PVDF、CMC、PTFE 质量比为 1:1:2。更小粒径的粘接剂能实现电极膜活性物质更 均匀的分布,与此同时,粒径更小的粘接剂有更强的粘连性。
(四)PTFE 竞争格局及价格
山东东岳是最大的 PTFE 生产厂商。山东东岳、中昊晨光、浙江永和、巨化集团是国内 排名前四的聚四氟乙烯生产商,行业竞争格局较为稳定。
国内企业生产的 PTFE 的下游应用主要集中于低端塑料产品,高端 PTFE 主要依靠进口。 高端 PTFE 用于 5G 通讯以及干电极,当前产能集中于外企如杜邦、大金等。目前,我国 低端 PTFE 产能尤为过剩,也导致其价格的不断下降,但伴随氟化工龙头逐步转型布局 高端 PTFE,在干法电极成熟后龙头企业有望充分享受行业红利。
(五)高端 PTFE 需求蓝海市场
全面替代湿法电池打开 PTFE 需求想象空间。新能源产业在各国发展如火如荼,在储能 侧、动力侧以及 3C 领域的拉动下,预计全球锂电池的需求将以 30%以上的增速逐年增 加。锂电池需求的高速增长也将打开干电极以及其粘接剂 PTFE 的想象空间。
干电极技术将带动 PTFE 需求快速增长。传统湿法电池中,正极粘接剂采用 PVDF,质 量占比 2%;负极粘合剂采用 CMC+SBR,质量占比 3%。干法工艺中,PTFE 同时适用于 正极和负极,质量占比提升至 5~8%,在干法工艺渗透率逐步提高的背景下,干电极 PTFE 的需求增速较 PVDF 能实现 4 倍的增长。我们预计 2025 年干法电极渗透率达到 3%,2030 年达到 15%,2030 年干电极 PTFE 总需求达到 21.91 万吨。
5G 通讯所需 PTFE 出货量稳定增长,干电极成熟后将贡献核心增量。高端 PTFE 广泛应 用于 5G 电子通讯领域。PTFE 绝缘性优异,不易被高频电波干扰,含氟聚合物在高频条 件下具有良好的低介电性能、低损耗因子,能够为数据中心、信号发射塔及个人电子设 备提供超高频和高速性能,目前需求稳定增长。假设 2030 年干电极渗透率 15%,则干电 极所需 PTFE 将占据七成高端市场份额。 预计干法电极将在 2025 年后逐步铺开,我们假设 PTFE 平均单价 5.20 万元/吨,预计高 端 PTFE 的市场价值在 2025 年达到 27.83 亿元,2030 年达到 161.86 亿元。
三、加工设备:干法工艺提升辊压要求,压延切边一体是制膜发展方向
(一)干法制膜装置:自支撑膜制造设备
主流的自支撑膜制造设备分为气流粉碎机、螺杆挤出机以及开炼机。气流粉碎机效率最 高,螺杆挤出机良率最高。
气流粉碎机的工作原理是,压缩空气通过喷嘴高速射入粉碎腔后,活性物质及粘接 剂混合物通过进料口到达粉碎腔。混合物在高压气流的作用下相互碰撞粉碎实现原 纤化,最后,混合物随气流上升至分级腔在辊压设备作用下形成自支撑膜。气流粉 碎机的工作效率最高。
螺杆挤出机的工作原理是,混料自料口进入螺杆充满螺槽后,会在旋转的螺杆作用 下在料筒内壁和螺杆表面不断被压实、搅拌以及混合。在压缩段结束处,螺杆会将 混合均匀的物料按要求挤出机头,在机头中混合物会被塑成电极膜并送离挤出机, 螺杆挤出机的良率最高。
开炼机的工作原理是,两个相对回转的辊筒对物料产生挤压后,由于两个辊筒的速 比不同,因此可以产生对混料产生剪切力,速比越大剪切力越强。在辊筒的高剪切 力下,混合物内部的分子链会被打断,实现均匀的混合,多次往复后在粘接剂原纤 化的作用下即生成电极膜。
(二)干法电极设备迭代:辊压设备
干法工艺较湿法对辊压设备的工作压力、辊压精度以及均匀度提出更高要求。头部辊压 设备厂商或率先受益于干法电极对于新型辊压机的迭代需求。
4680 干法正极需要更大压实力度的辊压机。当前特斯拉 4680 电池仅在负极使用干电极 技术。在正极干法的制作过程中,正极自支撑膜辊压后容易掉粉,需要有更大外部压力 抵消粉末间的复合力。SACMI 2000 系列辊压机在压实力度、精度以及辊压一致性上比较 优秀,或是解决正极干法问题的方案之一。
(三)干法制膜发展方向:设备大型化集成化,压延切边一体化
设备大型化集成化是未来发展趋势。将加料、混料、纤维化、制膜、辊压、分切、收卷等 功能集成在一起,降低流转时间,提高效率及一致性等,设备价值量更高。特斯拉采用的压 延切边一体机的辊压部分类似开炼机。在机器的头部放料后,混料会沿着走带方向进入 辊筒,由于下游的辊筒转速快于上游,辊缝间形成的高剪切力会对活性物质、导电剂以 及粘接剂挤压并混合。在原纤化作用下形成的自支撑膜会附着到下游更快的辊筒上并反 复压延。机器侧边的计量辊可以控制辊筒的转速和温度,而在机器的尾部会设置分切系 统,将成型的宽电极膜按要求裁切成窄电极膜。双面涂层与集流体复合层压机器是集合 正/负电极膜生产、电极膜和集流体层压和极片收卷,本质是压延切边复合一体机。
新能源汽车的快速发展带动了动力电池的高速增长。动力电池生产流程一般可以分为前段、中段和后段三个部分。其中,前段工序包括配料、搅拌、涂布、辊压、分切等,中段工序包括卷绕/叠片、封装、烘干、注液、封口、清洗等,后段主要为化成、分容、PACK等。材料方面主要有正负极材料,隔膜,电解液,集流体,电池包相关的结构胶,缓存,阻燃,隔热,外壳结构材料等材料。 为了更好促进行业人士交流,艾邦搭建有锂电池产业链上下游交流平台,覆盖全产业链,从主机厂,到电池包厂商,正负极材料,隔膜,铝塑膜等企业以及各个工艺过程中的设备厂商,欢迎申请加入。
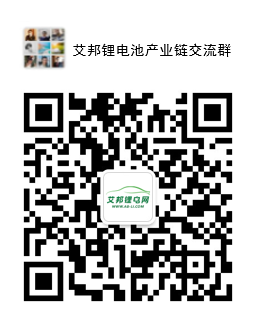
长按识别二维码关注公众号,点击下方菜单栏左侧“微信群”,申请加入群聊