2020年我国提出了“碳达峰”和“碳中和”的目标,发展高效、廉价、安全的储能技术是实现这一目标的关键。在众多的储能技术之中,锂离子电池受到了最多的关注,且已被广泛应用于便携式电子产品、新能源汽车、规模储能等领域。随着我国能源战略的变化和新能源产业的飞速发展,人们对锂离子电池的能量密度和安全性都提出了更高的要求。
为了获得更高的能量密度,产业界追求使用具有更高理论比容量的电极材料(如高镍三元正极、硅碳负极以及金属锂负极),但这类材料的热/化学稳定性更差,提升锂离子电池能量密度的同时往往牺牲了其安全性。
因此,如何在提高电池能量密度的同时也能保证其安全性,已经成为了制约锂离子电池发展的一大难题。
电池能量密度的提升与其质量密切相关,通过减少电池中的非活性组份(如隔膜和集流体等)用量已经成为科研界和产业界的研究热点。集流体作为正极材料和负极材料电子传输的载体,在电池的充放电过程中并没有提供任何的容量,同时,铝箔和铜箔的密度均较大,这种存在于电池内的“死质量”严重影响其能量密度。
因此,如何用更轻的材料去取代传统的金属集流体是提高电池能量密度发展的一个重要方向。最近,斯坦福大学的崔屹等采用原位聚合和磁控溅射的方法制备了具有阻燃作用的聚酰亚胺镀铜膜,当采用该膜作为负极材料的载体时,其能量密度能提高26%。
此外,伦敦大学Pham和美国宇航局Darst等报道了基于金属化塑料集流体在18650电池中有效地抑制了电池在针刺测试下的热失控。这些报道说明了高分子复合金属集流体在改善锂离子电池的安全性和提升电池的能量密度上都有非常明显的的优势。尽管这些报道从实验的角度验证了复合集流体在电池中的巨大潜力,但是规模化的制备以及应用仍然是一个值得商榷的问题。
卷对卷工艺制备的复合金属镀膜已广泛应用于包装、电容、电磁屏蔽和印刷电路板等领域。其中,以聚对苯二甲酸乙二醇酯(PET)和聚丙烯(PP)薄膜为代表制备的镀铝复合膜在包装领域占有巨大的市场,这种通过蒸镀工艺制备的镀铝复合膜具有良好的金属特性。
与传统的铝箔相比,这种基于物理气相沉积制备的复合膜其高分子基材与金属镀层之间具有较差的结合力,导致金属镀层容易从基材表面脱落,这将严重影响复合膜在电池中的长期稳定性。
在包装薄膜领域,等离子体处理是工业上广泛使用的技术,对膜材表面进行处理后能改善其粗糙度,从而加强基材与镀层之间的结合力。但是基于这种策略制备的复合膜作为集流体被应用在锂离子电池中时,在电解液环境体系下金属层与高分子层结合力不佳将会引发较严重的金属脱层、金属层龟裂且不连续、不均匀,这些行为都将大幅度降低电极材料的导电性,增大电池的内阻,从而引发电池的安全问题。
纳米氧化铝与氧化硅常被用于高附着力和高阻隔性包装材料,已经实现了规模化生产,且广泛应用于食品、药品、电子等包装领域。氧化铝和氧化硅两种材料作为已成熟应用到PET作为基材的包装材料中,可通过机械互锁作用和化学键合来提高高分子材料与金属层界面结合力。
此外,Drabold等通过轨道量子化动力学理论研究高聚物对铝和无定形氧化铝表面的粘结作用,发现氧化铝层的引入,使得PMMA基材中的羰基的氧与氧化铝中的Al原子形成O-Al强离子键。同样地,氧化硅在沉积过程中与PET表面的含氧官能团形成化学键合,从而提升界面结合力。
为了解决复合集流体在电解液中脱层的问题,本文采用卷对卷的工艺制备了含有氧化铝或氧化硅中间层的复合镀铝膜。分析了两种膜材在高温下电解液兼容性的差异。此外,在针刺测试中,氧化铝复合镀铝膜制作的软包电池表现出了优异的安全性能。我们的发现为复合集流体在锂离子电池中的应用提供了理论指导和解决方案。
长按识别二维码关注公众号,点击公众号下方菜单栏左侧“微信群”,申请加入群聊
如图 1所示,复合集流体具有典型的三明治夹心结构。首先将PET (厚度为12 μm,由东丽株式会社提供)作为支撑基材,在PET基材双面采用纳米氧化硅或纳米氧化铝作为中间强化层,Al为上下表面导电层。
图 1. 复合集流体制备过程(X为AlOx或SiOx)
具体地,PET-SiOx复合薄膜由无锡泓瑞航天科技有限公司提供(PECVD沉积,厚度50–100 nm);PET-AlOx复合薄膜通过在PET基材上蒸镀纳米氧化铝得到(PVD电阻加热沉积,厚度50–100 nm);Al导电层(铝丝由海宁精诚铝业有限公司提供)通过电阻式真空蒸镀沉积(图 2)在PET-SiOx或PET-AlOx复合薄膜上。
图 2. 分步式卷对卷真空蒸镀沉积示意图
受选用的高分子基材PET的耐温性限制,其热熔融温度为212–265℃,热变形温度为75℃,采用的电阻蒸发时蒸发舟温度达到1300–1600 ℃,因此为了保证PET基材不受热形变,蒸镀铝过程中必须保证较快的膜运转速度和一定的送丝速度。
因此根据生产经验,单层厚度在50–100 nm之间PET基材不会出现打皱和卷曲形变现象,铝层蒸镀表现平整。为满足集流体导电性能需求,需要通过多次分步式蒸镀法沉积厚度度至700–800 nm,具体的分步式蒸镀工艺参数见表 1。
表 1 分步式卷对卷真空蒸镀沉积工艺
采用四探针方阻仪测试蒸镀后的导电层方阻,利用TSE504C型电子万能试验机进行复合膜的机械性能测定,采用Thermo ESCALAB 250XI (赛默飞) X射线光电子能谱射线衍射仪(XPS)对表面成分进行分析表征,采用德国Bruker Dimension ICON的原子力显微镜(AFM)进行微观形貌表征(测试条件为扫描速率3.07 Hz,振幅定位点378.41 mV,驱动振幅50 mV),采用赛默飞Helios G4-UX型聚焦离子束FIB (SEM)进行样品切割和形貌观察,通过EDX能谱分析对制成的材料进行成分分析。通过乙烯-丙烯酸共聚物(EAA)剥离测试技术进行结合力测试。
集流体在电池环境中使用,必须具备良好的兼容性。目前商业化的锂电池中的电解液绝大部分是以LiPF6为电解质的有机溶液。LiPF6最大的缺点是热稳定性差和对湿度的高敏感性。在电解液配置及电池组装过程中不可避免会存在微量的水分,会促使LiPF6分解,产生POF3、HF等物质。HF对于铝集流体和正极活性物质本身具有腐蚀作用。
因此为探究其电解液中兼容性能,我们设计了模拟充盈电解液状态下的极端电池软包环境,分别进行了25、60和85 ℃三个温度环境下浸泡72 h的复合集流体和其制成极片的兼容性试验,其中极片为三元LiNi0.5Co0.2Mn0.3O3 (NCM523)正极。
电解液为1 mol∙L−1 LiPF6在体积比为1 : 1 : 1的碳酸乙烯酯/碳酸二甲酯/碳酸乙酯(EC/DMC/EMC)中加入1%的碳酸乙烯酯(VC)添加剂作为电解质。
对通过电解液兼容性试验的集流体组装电池进行测试分析。
对使用了PET-AlOx-Al复合集流体和Al箔集流体的200 mAh的软包电池进行针刺试验,将电池充电至4.2 V、100%充电深度状态下使用DMS-ZC针刺试验机(中国东莞)进行针刺,选取直径为4 mm的不锈钢钉以10 mm∙s−1的速度刺穿软包电池,记录针刺过程中的电压变化。
集流体的导电性与电池的电性能息息相关。因此,我们采用四探针方阻仪对PET-Al、PET-AlOx-Al以及PET-SiOx-Al三组样品的复合集流体进行表面方阻的测定(表 3)。
从测试结果可以看出,三组样品实现较为一致的表面方阻,说明中间强化层的引入并不会影响复合集流体的导电性。
表 3 镀铝后不同复合集流体表面方阻
软包电池在生产制备过程中对集流体的力学性能具有较高的要求。通过对比不同中间强化层复合集流体的应力应变曲线图 3a,可以得到PET基材的拉伸强度为236 MPa图 3b,在其上下表面直接复合一层750 nm的铝层后拉伸强度下降为173 MPa。当引入约50 nm厚的氧化铝强化层后,其强度升高到188 MPa,氧化硅强化层的复合薄膜拉伸强度为212 MPa。
PET基材断裂伸长率135%,直接复合750 nm金属铝后断裂伸长率为70%,含有氧化铝强化层复合薄膜断裂伸长率98%,氧化硅强化层复合薄膜断裂伸长率128%。而直接复合金属铝后弹性模量由PET白膜的289 MPa增大到4027 MPa,而复合了中间氧化铝层的弹性模量为4359 MPa,氧化硅强化层为3835 MPa。
相较于无中间强化层的复合集流体,有氧化物中间强化层的复合集流体具有更好的力学性能,更有利于满足电池极片涂布和辊压过程的制备工艺。
图 3. 不同中间强化层复合集流体的力学性能:(a)应力应变曲线,(b)弹性模量,(c)拉伸强度,(d)断裂伸长率
通过对PET-Al、PET-AlOx-Al以及PET-SiOx-Al三个复合集流体样品进行EAA热封后的剥离力测试,结果(图 4)可以看出,PET直接镀铝的铝层EAA测试结合力为3.30 N,PET复合氧化硅中间强化层后镀铝的EAA剥离时结合力达4.39 N,而PET复合氧化铝中间强化层后镀铝的铝层剥离时结合力达6.03 N。
中间强化层的引入显著增加了基材与镀层之间的结合力,其中氧化铝强化层的铝基复合集流体的结合力最大,氧化硅次之。这是因为添加纳米粒子能改善高分子材料的多种性能,特别是高分子材料的表面粗糙度和表面能。纳米氧化物提升了高分子材料和金属界面机械互锁作用和引入了化学键合作用,表现出结合力的有效提升。
图 4. PET蒸镀铝与增加中间强化层复合集流体EAA结合力曲线
为了确认氧化物中间层的存在,我们对蒸镀有中间层的基膜进行了元素分析。通过XPS元素分析可知沉积在PET基材表面的中间氧化物分别为氧化铝和氧化硅。氧化硅与氧化铝与高分子基材表面的含氧活性官能团能形成稳定的化学键合(O―Al键和O―Si键),并且又能与表面蒸镀的铝形成强Al―O键,有效提升了整体界面稳定性。
图 5. 不同中间强化层复合集流体的XPS曲线:(a)氧化铝中间强化层表面元素的结合能谱图,(b)氧化铝中间强化层在更高分辨率下Al 2p的结合能谱,(c)氧化铝中间强化层在更高分辨率下O 1s的结合能谱,(d)氧化硅中间强化层表面元素的结合能谱图,(e)氧化硅中间强化层在更高分辨率下Si 2p的结合能谱,(f)氧化硅中间强化层在更高分辨率下O 1s的结合能谱
利用AFM观察氧化铝强化层的微观形貌,可以看到沉积后薄膜的表面粗糙度更大,有利于增大与铝层的接触面积,增加与铝层的结合力。通过计算可知,未经氧化物处理的PET平均粗糙度为0.996 nm,氧化铝表面的平均粗糙度为12.19 nm,氧化硅的平均粗糙度为3.53 nm。
结合AFM的三维图像(图 6)可以更加直观反映出氧化铝强化层的表面粗糙度要大于氧化硅,且两者相较未做氧化层处理地PET白膜粗糙度有明显提升。表面粗糙度的增大带来薄膜比表面积的增大,增加了界面的机械互锁作用,也为真空蒸镀的铝层提供更好的结合力。
图 6. (a,b) PET-AlOx薄膜AFM的3D和2D图像,(c,d) PET-SiOx薄膜AFM的3D和2D图像,(e,f) PET白膜AFM的3D和2D图像
用聚焦离子束对样品进行切割以便于观察截面形貌,并通过SEM可以看到样品呈现三层复合结构,中间厚度较大且较暗的为不导电的高分子PET基材,通过测量图 7a可得到其厚度为12 μm,上下两层较为致密的为真空蒸镀的铝层,单面厚度为700–800 nm,铝导电层由分步式蒸镀了14次铝层(单层厚度约50–60 nm)复合而成,在更高倍率下可以看到截面多层结构(图 7b),层与层之间沉积致密无缝隙,图 7c的多次蒸镀铝的颗粒大小均匀致密,有利于获得较高导电率。
图 7. 复合集流体SEM截面图:(a)复合集流体截面的整体结构微观图,(b)截面图,(c)复合集流体铝层表面形貌
比较(a、b) mapping能谱测试(图 8)可以发现,选取的为PET基材、氧化铝和表面铝层三层结构的区域,铝元素峰值最强,含量最高,分布在截面的上层区域。氧元素分别分布于表面和高分子基材与铝层中间区域,可推断除强化层复合生成的氧化铝强化层外,表面金属铝在空气中也局部氧化形成氧化铝保护层。
比较(c、d)可以发现,同样为三层复合结构,氧元素主要分布在基材与表面铝层中间,硅元素同样也分布在强化层。通过能谱可进一步确定氧化物强化层的沉积。
受工艺影响,AlOx中间层与表面铝层分界不如SiOx清晰。AlOx中间层制备是在铝蒸发的过程中通入氧气,使其反应形成纳米氧化铝沉积在PET薄膜表面,但因蒸发速度较快,存在不完全反应的Al与AlOx一同沉积。
因此氧化铝中可能含有部分Al,所以在能谱图中AlOx与表面Al导电层的分界无法清晰分辨,但AlOx与SiOx中间层厚度都在50–100 nm之间。
图 8. 复合集流体截面能谱图:(a) PET-AlOx-Al复合集流体截面元素分布,(b) PET-AlOx-Al复合集流体截面能谱,(c) PET-SiOx-Al复合集流体截面元素分布,(d) PET-SiOx-Al复合集流体截面能谱
电解液兼容性实验结果如图 9所示,PET基材直接复合金属铝层的结构中,金属与高分子薄膜基材界面稳定性差,界面结合力弱,易造成在电解液环境中金属层与高分子基材的脱层现象。复合了氧化物强化层后的三层结构则在电解液环境中的高温兼容性上有所提高。并且在制成极片后的耐电解液性能同时也得到提升。
由于在锂离子电池电解液环境中,水分的存在会与电解液中的LiPF6形成HF,而HF具有腐蚀性,易在PET-Al薄膜的金属-高分子界面反应,导致金属层的脱落;而在复合了中间氧化物强化层后,为金属与高分子材料提供了更多的锚点,同时化学键合也提高了界面的致密性,HF对其界面的腐蚀导致金属脱层现象得到有效缓解。
图 9. 电解液浸泡实验结果:(a,b,c)依次为PET-AlOx-Al集流体25、60及85 ℃下经过72 h的电解液浸泡结果,(d,e,f) PET-AlOx-Al复合集流体制成极片25、60及85 ℃下经过72 h的电解液浸泡结果,(g,h,i)为PET-SiOx-Al复合集流体25、60及85 ℃下经过72 h的电解液浸泡结果,(j,k,l) PET-SiOx-Al复合集流体极片25、60及85 ℃下经过72 h的电解液浸泡结果,(m,n,o)为PET-Al复合集流体25、60及85 ℃下经过72 h的电解液浸泡结果,(p,q,r)为PET-Al复合集流体制成极片25、60及85 ℃下经过72 h的电解液浸泡结果
通过对PET-Al、PET-AlOx-Al、PET-SiOx-Al三组集流体和其制成的极片电解液性兼容性试验,可以明显观察到无中间强化层的PET-Al复合集流体,经过25、60和85 ℃下72 h的电解液兼容性浸泡实验后,表面铝层发生了鼓泡、龟裂及脱落现象,取出后可明显观察到已暴露出透明基材,且其制成的极片也逐步发生了鼓泡和脱层现象,电解液兼容性差。
在复合了氧化硅中间强化层后的PET-SiOx-Al集流体和其极片的电解液兼容性都所有改善,在高温下集流体表面有鼓泡现象,但并未剥离,其极片表现则是在边缘区域有轻微的脱落掉粉现象;而复合了氧化铝中间强化层的PET-AlOx-Al集流体及其极片表现出最佳的电解液兼容性,在经过25、60和85 ℃下72 h的实验浸泡后集流体表面没有受到侵蚀现象,铝层完好且平整,与基材和中间强化层还保有良好的结合力,由其制成的极片也展现出一致良好的电解液兼容性,尤其极片在辊压后,未发生活性层的剥离和脱落,且较为平整。
这是因为电池体系中易存在微量的水,水与电解液中的LiPF6发生反应产生HF,而氧化铝与氧化硅均与HF发生反应。但是氧化硅比表面积较大,表面羟基丰富,氧化硅与金属间的作用较弱。
相比之下氧化铝的热稳定性好、比表面积适中、与金属之间的作用较强。比较氧化铝和氧化硅与氢氟酸反应活性,有研究证明,溅射的氧化铝保护层在60 ℃下HF的侵蚀60 min后氧化铝的厚度并没有改变。同样地,采用HF分别刻蚀氧化硅和氧化铝,两种热氧化物与HF反应速率明显不同,HF刻蚀氧化硅的速率远大于氧化铝。
因此,氧化硅强化层的电解液兼容性差于氧化铝强化层。
为进一步验证氧化铝强化层对HF腐蚀的抑制作用,分别将PET-AlOx-Al复合集流体与PET-Al集流体与金属锂片组装成扣式半电池,测试其电化学阻抗,通过阻抗大小反应其耐腐蚀效果。
验证结果如图 10所示,缺少了界面强化的复合集流体在电解液中HF的腐蚀下导致Al与PET脱层,龟裂现象,导致欧姆阻抗的增加。氧化铝层在电解液环境中对界面的强化作用有效缓解HF对复合集流体的侵蚀。
图 10. PET + Al和PET-AlOx-Al集流体85 ℃三天后阻抗谱图
经过电解液兼容性试验,本研究筛选出界面强化效果最佳的PET-AlOx-Al复合集流体与Al箔集流体制备出软包电池,电性能进行分析表明此PET-AlOx-Al复合集流体完全适应目前现有的电池制备技术,且对电池的电化学性能没有影响。
图 11. 使用PET-AlOx-Al复合集流体和Al集流体软包电池循环性能:(a) 0.2C倍率下循环性能,(b)充放电曲线
对使用了PET-AlOx-Al复合集流体和Al箔集流体的200 mAh的软包电池进行针刺试验。电池为100%充电深度状态,电压达到为4 V。如图 12所示,使用Al箔集流体的软包电池(黑色部分)在针刺后立即发生短路(电压降至0 V),而使用了PET-AlOx-Al复合集流体的电池(红色部分)在针刺后电压基本还可维持在4 V,且无起火冒烟现象,有效阻止了电池的内短路。
图 12. 使用PET-AlOx-Al复合集流体和Al集流体软包电池针刺时的电压变化曲线
通过在PET高分子基材上分别复合氧化铝和氧化硅两种涂层作为强化层,可提高金属铝与高分子基材的结合力。强化层的引入并未影响铝层的表面方阻,保证了复合集流体在电池中的正常使用。
纳米氧化铝与氧化硅可显著增大高分子基材表面的粗糙度,提供界面化学键合,明显提升了高分子基材与铝层的结合力。
结合力的提升有利于复合集流体抵抗电解液的侵蚀,通过电解液兼容性实验进一步分析得知,氧化铝强化层与HF的反应活性低于氧化硅强化层,表现出更佳的电解液兼容性。
使用氧化铝强化层的PET-AlOx-Al复合集流体电池性能与使用商业化的Al箔锂电池相似,可较好地适应现有电池制备技术。且经过氧化铝界面强化后的复合集流体对电池针刺安全起到了巨大的提升作用,抑制了电池针刺过程的内短路。
文章来源:汪茹, 刘志康, 严超, 伽龙, 黄云辉. 高安全锂离子电池复合集流体的界面强化[J]. 物理化学学报, 2023, 39(2): 220304.

新能源汽车的快速发展带动了动力电池的高速增长。动力电池生产流程一般可以分为前段、中段和后段三个部分。其中,前段工序包括配料、搅拌、涂布、辊压、分切等,中段工序包括卷绕/叠片、封装、烘干、注液、封口、清洗等,后段主要为化成、分容、PACK等。材料方面主要有正负极材料,隔膜,电解液,集流体,电池包相关的结构胶,缓存,阻燃,隔热,外壳结构材料等材料。 为了更好促进行业人士交流,艾邦搭建有锂电池产业链上下游交流平台,覆盖全产业链,从主机厂,到电池包厂商,正负极材料,隔膜,铝塑膜等企业以及各个工艺过程中的设备厂商,欢迎申请加入。
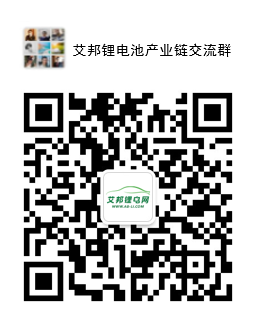
长按识别二维码关注公众号,点击下方菜单栏左侧“微信群”,申请加入群聊