# X-Ray检测 #
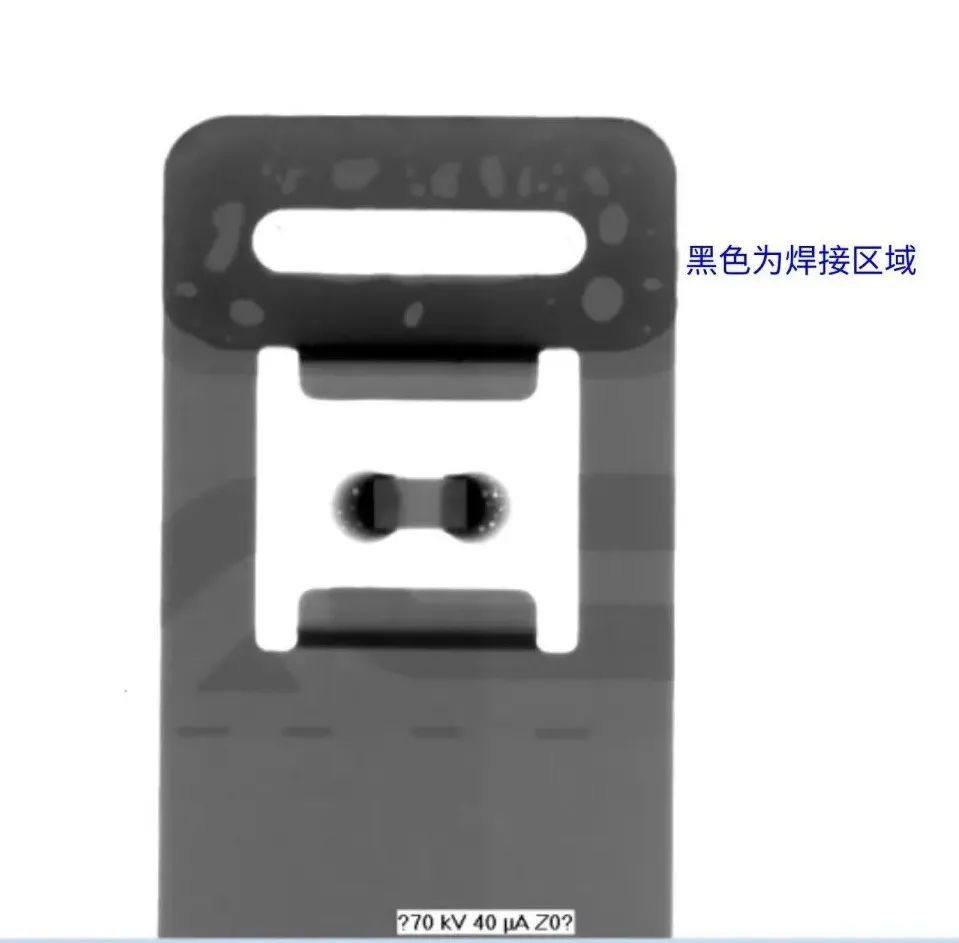
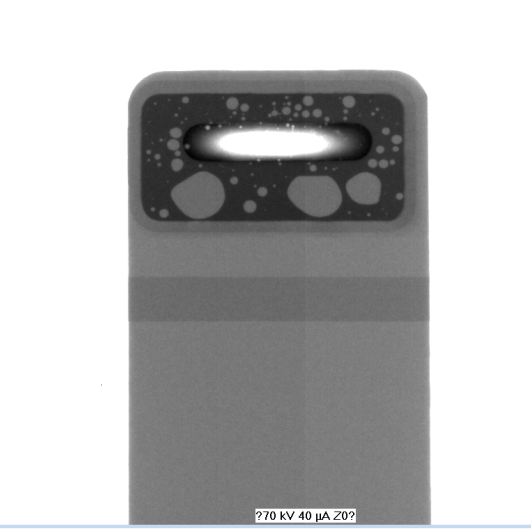
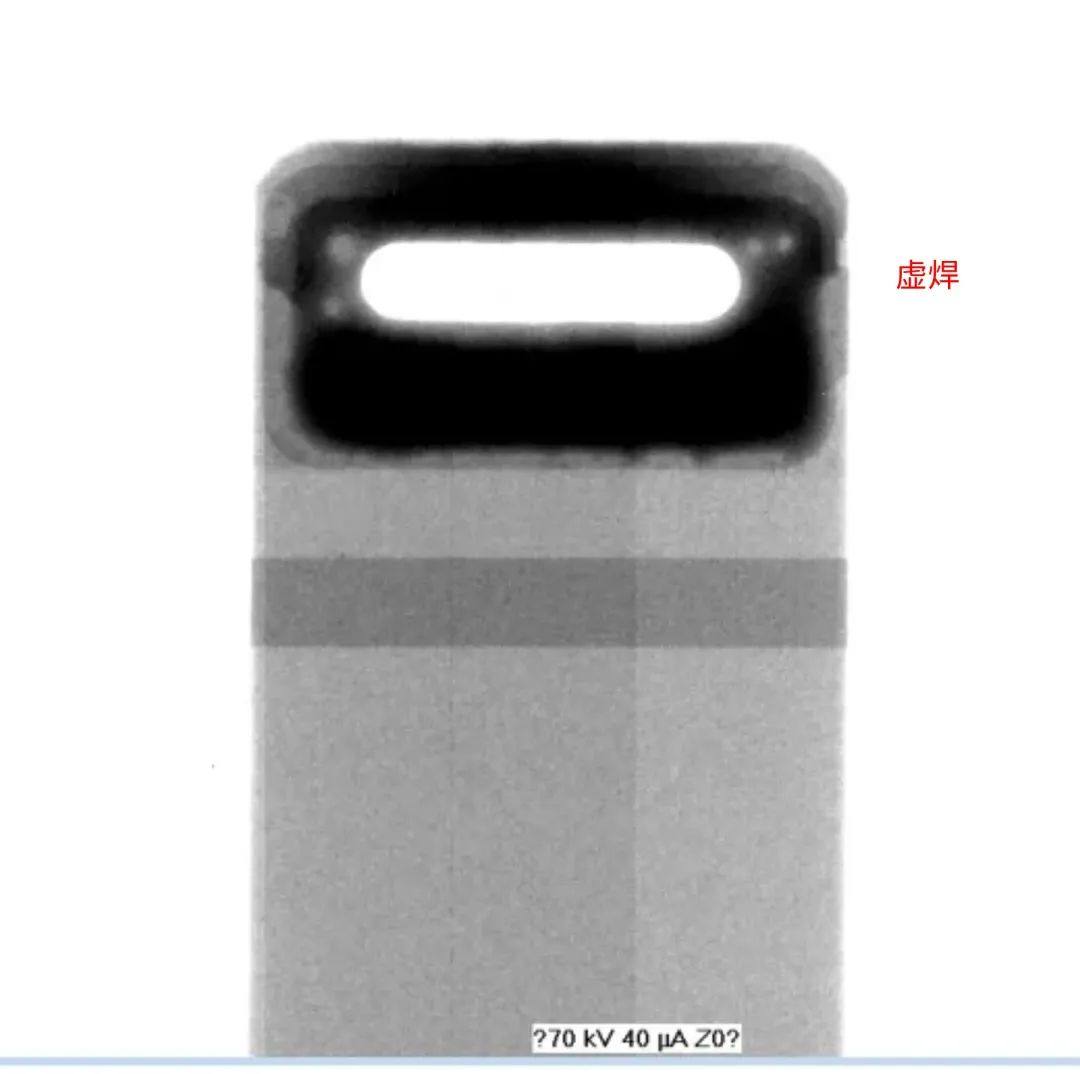
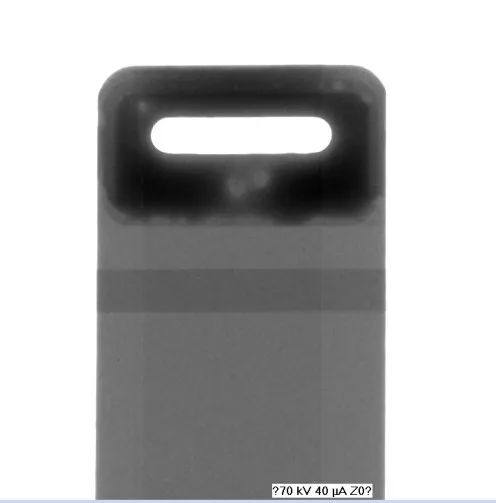
#失效焊点的剥离表面分析#
- Ni片焊接剥离面Sn为自然聚合状态,表面光滑,无拉扯或锯齿状态。
- FPC pad面偏灰色,表面光滑,有明显坑状气泡空洞痕迹,无拉扯或锯齿状态。
- 通过SEM分析显示,pad表面平整,结晶规则。整体呈现灰白色,结晶颗粒约2μm左右。
- EDS分析结果显示,pad面主要以Sn、Cu金属成分构成。C、Cl主要来自于剥离面的附着物,据此判断为助焊剂残留物。同时,Sn、Cu元素产生了相互熔合渗透。
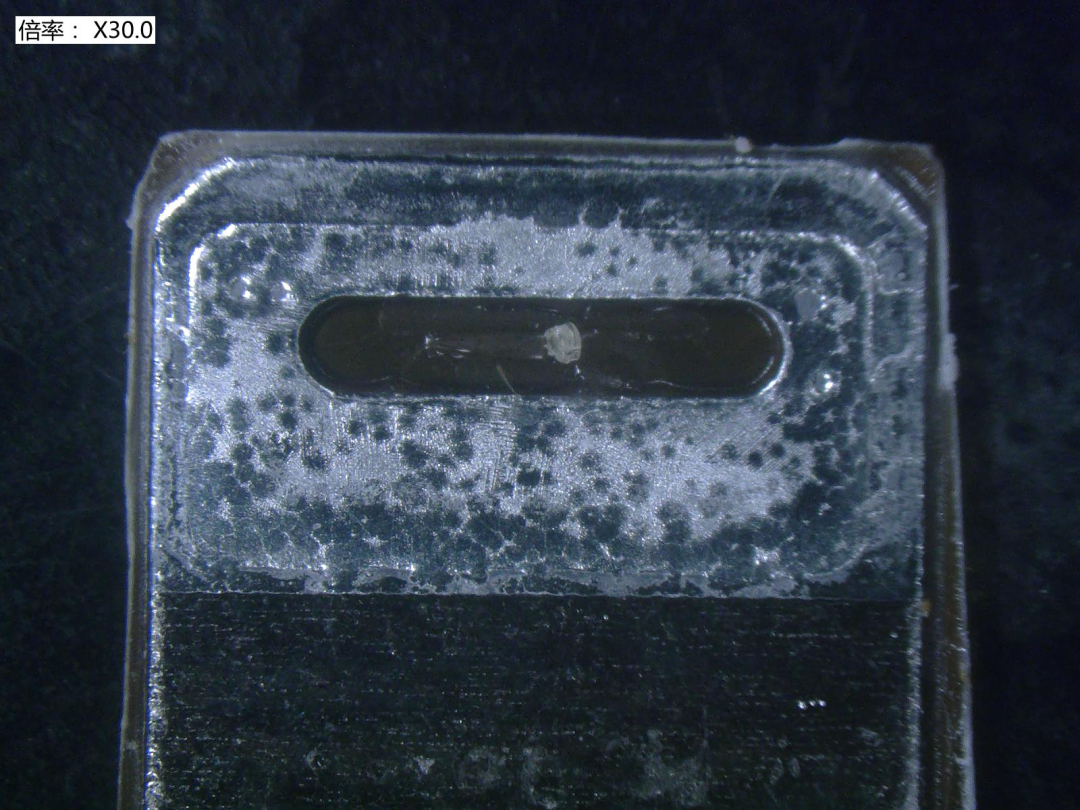
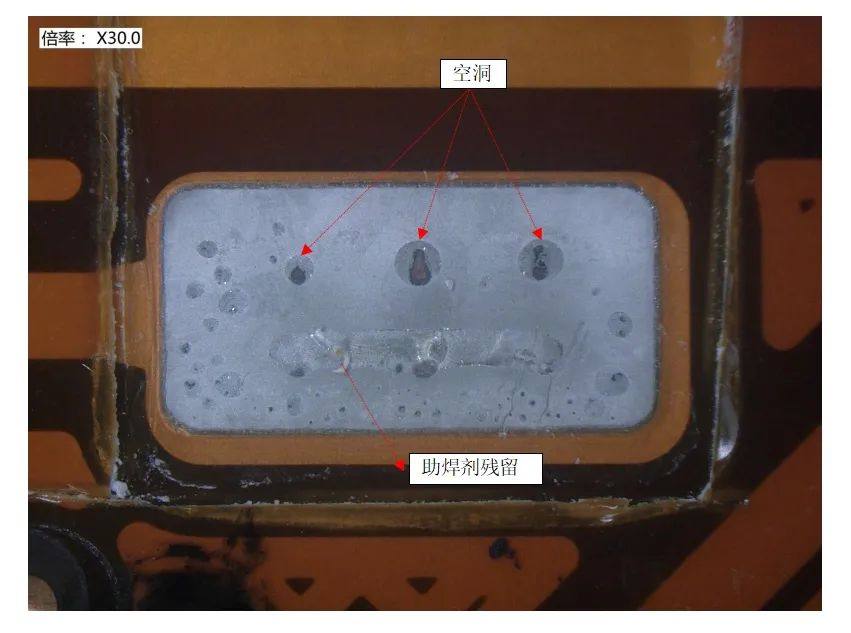
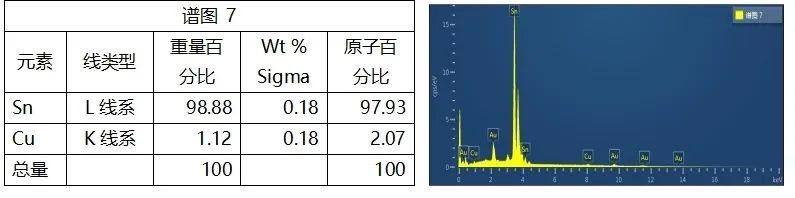
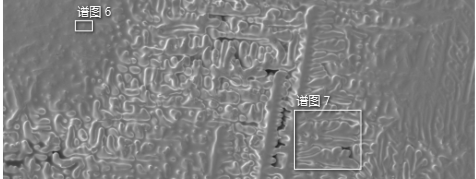
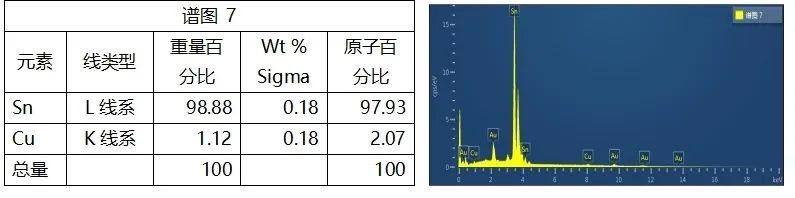
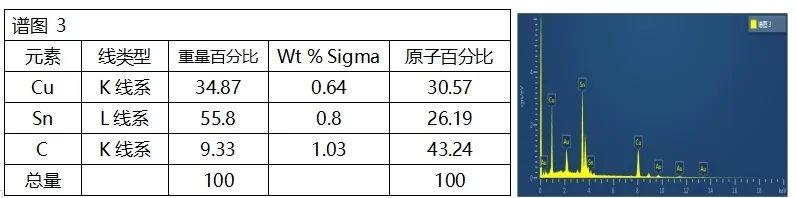
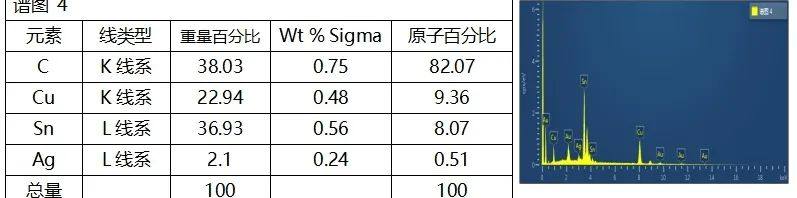
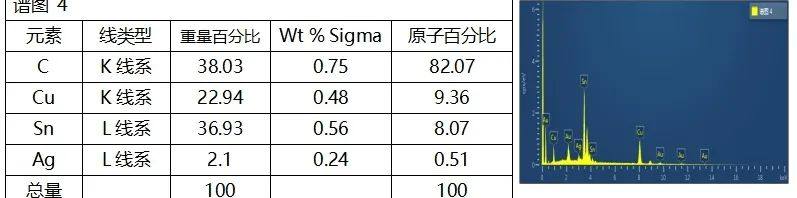
#失效焊点的切片断面分析 #
分析发现:
- 断面金相分析发现:Sn与FPC pad分离,FPC pad铜面弯曲变形。焊锡呈自然的凝聚弧形状态。从其整体状态判断,内部受到了热应力作用即热膨胀。
- SEM分析发现:焊点断裂面位于Sn与pad侧的IMC层,断点在IMC层整体贯穿。IMC层整体连续、均匀,厚度2.0μm左右,状态良好。部分Sn面呈自然凝结弧状。
- EDS分析发现:pad上的IMC层以Cu、Sn构成,重量比约为40:60,为Cu6Sn5结构,是良性IMC。断裂面的焊锡侧为100%Sn成分,进一步说明断裂面为Sn与pad侧的IMC层。
- Ni片侧、pad侧的Sn结晶状态无明显差异,说明焊锡过程是同步的。
- 在断面上检出较明显的助焊剂残留。
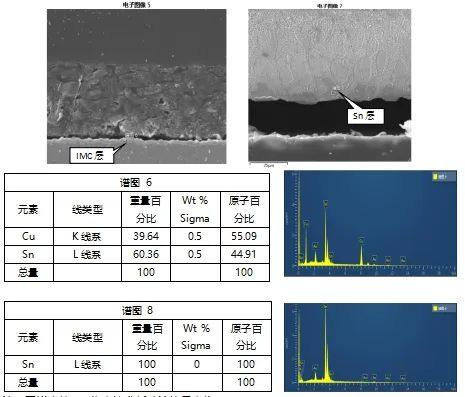
#良好焊点的切片断面分析#
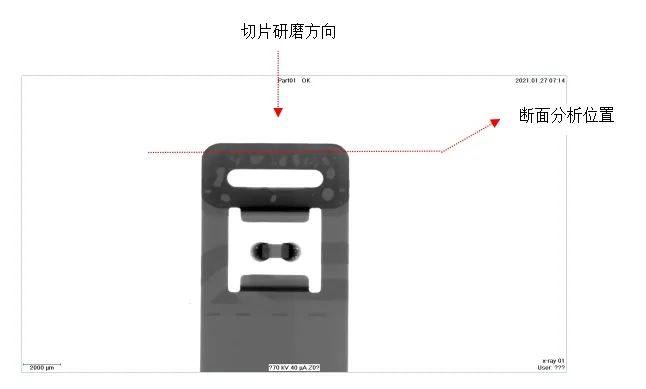
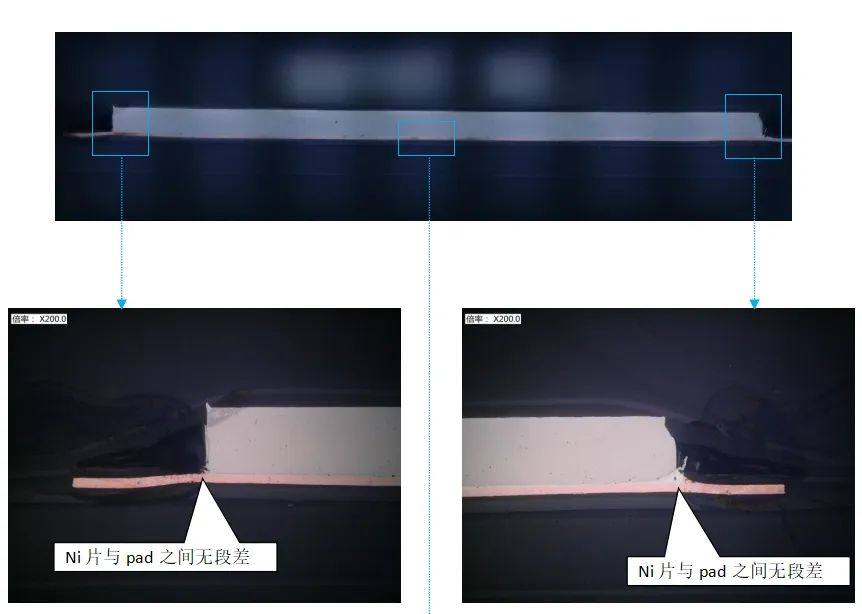
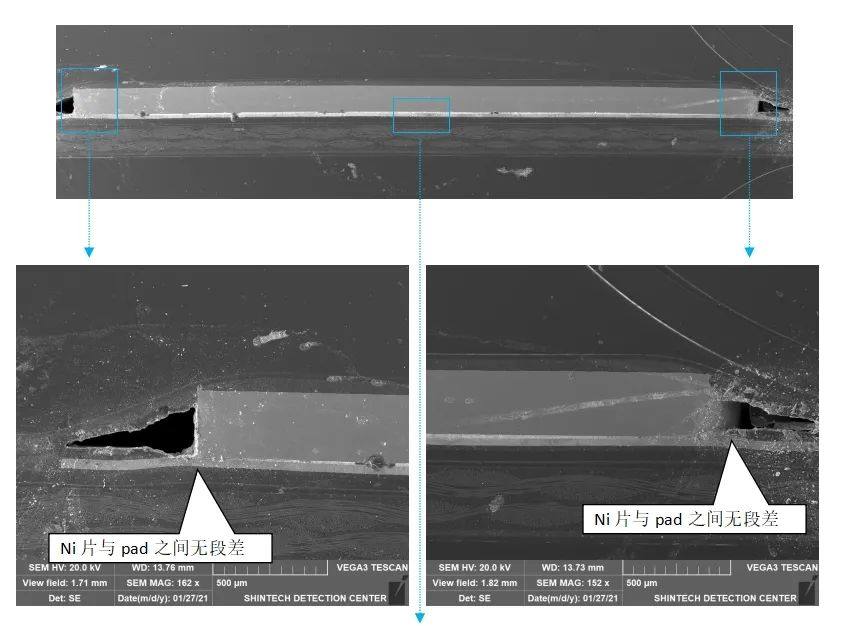
#FPC pad与Ni片组装结构#
- 部分FPC pad相对平面有50μm-60μm的段差,即下沉,部分无段差。
- 工艺流程:Ni片SMT回流焊接→PI膜→SMD元件焊接,即Ni片在PI膜贴附后还要回流一次。
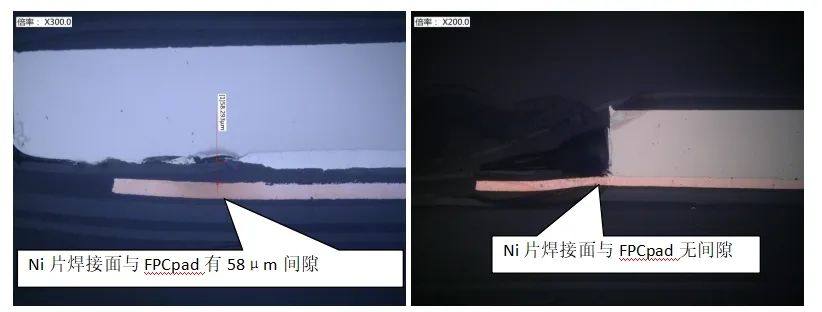
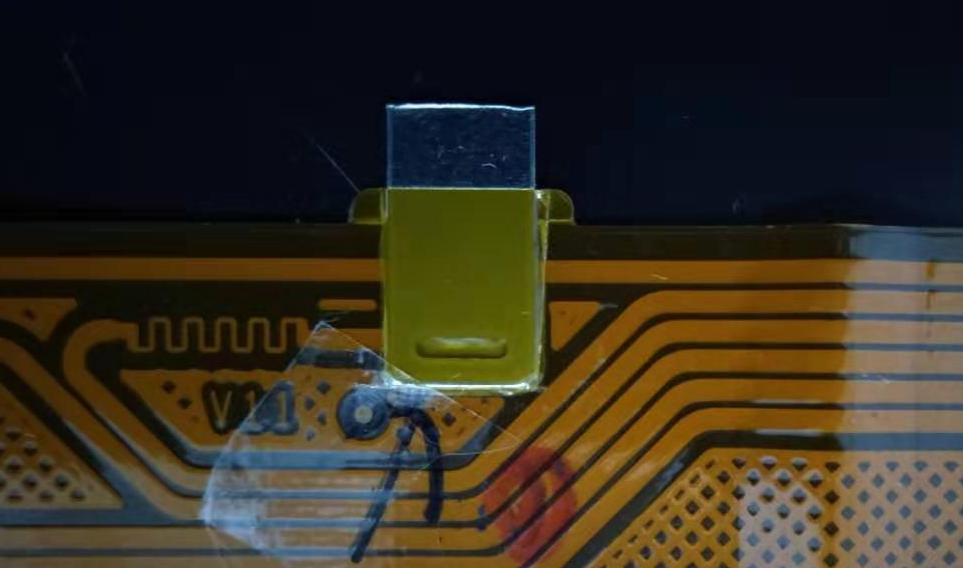
从虚焊点的平面与断面的分析结果可以判断——Ni片与FPC pad第一次回流焊接形成了良好的IMC层,焊接成功。焊接失效现象发生在后续工艺之中。
- FPC pad断面平滑,Ni片上附着的Sn表面及切面均呈自然冷却形成的弧状形貌。
- 虚焊面在Sn与IMC层之间。
- 失效焊点空间均呈热膨胀状态。
- FPC失效焊点的pad下沉约60μm,Ni片与FPC上的PI膜之间形成了应力集中点,如以下对比图所示——在热膨胀作用时,第一种状态容易受到热应力。
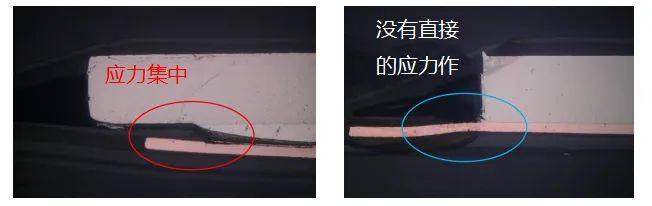
- 焊接点存在较大面积的空洞(最大75%左右),且有助焊剂残留。
- PI膜工艺使Ni片和FPC的焊接点形成了完全密闭的空间。在第二次回流焊时,会造成焊接挥发的气体无法排除,从而在内部形成热胀空间。
- 由于该产品的工艺特点,焊锡在第二次SMT时会再次经过熔化到冷却的过程。Sn与Sn之间的亲和性远高于Sn与IMC层之间的亲和性。
由于该FPC组装工艺的限制,在密闭空间内的焊点二次熔化时,焊点内部存在的空洞及助焊剂残留挥发物再度受热膨胀。
同时由于FPC本身的造成的段差,即与Ni片接触的PI膜,热膨胀对Ni片边缘产生应力,综合引起FPC铜面受力变形下陷。
并且由于焊锡的亲和作用,Sn与IMC层产生了自然分离,故形成虚焊。
建议措施
FPC 焊盘改善为无段差结构,Ni片与焊盘直接接触。
目的
保障锡膏印刷质量;
减少焊接时的热应力。
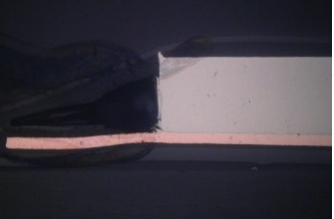
建议措施
每批次FPC板在上线前烘烤。
目的
除去内部湿气,避免焊接时的内部湿气释放,形成热应力。
建议措施
建议钢网厚度由0.08mm变更为0.11mm;
现状钢网开口的排期通道设计不足:
①排气通道由0.2mm变更为0.25mm;
②开口图形建议如下:
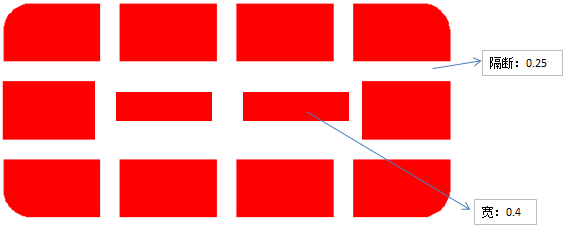
①增加锡量;
②增加焊接时的排气性,减少焊接空洞;
③减小第一次回流焊接时的虚焊隐患;
建议措施
对第一次回流焊接时的温度做整体评估。
目的
减少焊接空洞。
建议措施
Ni片焊接后,对孔内及边缘部分残留的助焊剂进行清洁。
目的
减少助焊剂残留,从而减少二次焊接时产生挥发性气体;
PI膜的密封性设计改善
建议措施
建议Ni片孔位置不封PI膜,在二次回流后采用密封电阻的方式,点胶密封。
目的
避免形成密封空间,导致内部热应力无法释放。
来源:新阳检测中心
新能源汽车的快速发展带动了动力电池的高速增长。动力电池生产流程一般可以分为前段、中段和后段三个部分。其中,前段工序包括配料、搅拌、涂布、辊压、分切等,中段工序包括卷绕/叠片、封装、烘干、注液、封口、清洗等,后段主要为化成、分容、PACK等。材料方面主要有正负极材料,隔膜,电解液,集流体,电池包相关的结构胶,缓存,阻燃,隔热,外壳结构材料等材料。 为了更好促进行业人士交流,艾邦搭建有锂电池产业链上下游交流平台,覆盖全产业链,从主机厂,到电池包厂商,正负极材料,隔膜,铝塑膜等企业以及各个工艺过程中的设备厂商,欢迎申请加入。
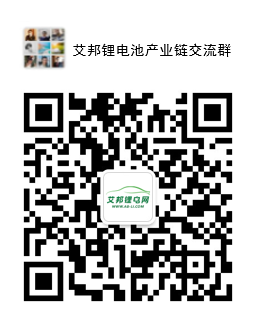
长按识别二维码关注公众号,点击下方菜单栏左侧“微信群”,申请加入群聊