
2017年前后,柔性印刷电路(FPC)刚刚开始在动力电池行业应用。由于初期生产成本较高,且汽车电子行业对可靠性要求严格,许多动力电池公司当时仍处于观望状态。随着柔性印刷电路的优异性能逐渐显现,以及大规模生产的成本迅速下降,用柔性印刷电路替代传统线束的进程明显加快。公开信息显示,特斯拉、国轩高科、中创新航、塔菲尔、欣旺达、孚能科技等公司均已开始使用柔性印刷电路。目前,柔性印刷电路解决方案已成为大多数新能源汽车的首选。
柔性印刷电路解决方案正朝着集成CCS(电池连接系统)的方向发展,结合塑料结构件、铜铝排等组件,形成电气连接和信号检测的结构件。采集线是电动汽车电池管理系统(BMS)的重要组成部分,用于监测动力电池电芯的电压和温度。它可以连接数据采集和传输,并具有过流保护功能。当发生异常短路时,它可以自动断开以保护电芯。
此前,新能源汽车的动力电池采集线通常采用传统的铜线束解决方案,但在处理大量电流信号时,铜线束会占用大量空间。在电池包组装过程中,传统线束依赖人工将端口固定到电池包上,自动化水平较低。相比之下,柔性印刷电路具有高集成度、超薄厚度和超柔软性等特点,在安全性、便携性、布局等方面具有突出优势。
柔性印刷电路在软包电池和硬包电池中的应用有所不同,不同厂商的做法也不同,包括不同的终端形式,如压接、焊接等。柔性印刷电路的最大优势在于其灵活性。随着电池控制技术的升级,它们可以演变成多种形式,并且可以定制。
此外,柔性印刷电路厚度薄,电池包结构可定制。在组装过程中,可以通过机械臂抓取并直接放置到电池包上,自动化程度高,适合大规模生产。用柔性印刷电路替代铜线束的趋势非常明显。
-
安全性能
在替代弱电线的同时,柔性印刷电路使用金属板连接母线,并增加保险丝保护电流设计,以确保高速信息传输路径,确保了即使电池包内部发生短路问题,柔性印刷电路的内部设计也会直接将电路铜线熔断,避免电池包其他部分发生燃烧或爆炸。
-
轻量化
与用于信号采集的传统线束和刚性PCB产品相比,柔性印刷电路在电池包中占用的空间更少,整体重量更轻。在整车中使用时,与线束解决方案相比,可减少约1kg的重量。
-
工艺灵活性
与传统线束的多个插入点和复杂的手工插接工艺相比,柔性印刷电路突破了工艺选择的限制。该产品可以结合电池包的特点,选择超声波、焊接等多种工艺;在线路区域厚度(0.34mm,NTC处为2mm)和灵活性(可实现90°、180°折弯组装)方面具有优势。
-
自动化生产
由于装配快速且精准,有利于实现自动化。在装配方面,可以避免线束设计中的许多人为错误,并减少连接器级别的错误插入。柔性电路板形状规则,设计集成度更高,可以节省大量布线和连接工作。它们适合大规模机械量产,大大减少组装时间并节省人力,同时为动力电池组装过程的自动化奠定基础。这进一步推动了动力电池市场对FPC的需求,因为柔性解决方案在现代动力电池制造中不可或缺。
在智能汽车时代,柔性电路板在电池上的广泛自动化应用是未来发展的趋势。从长远来看,随着技术升级,车辆中的许多低压线束单元可能会逐渐被取代,尤其是在对信号抗干扰要求越来越高的智能汽车中。主板和从板的电路甚至可能被芯片取代,这些芯片可以安装在柔性电路板上,以提高产品稳定性、节省空间并降低成本(尽管成本优势尚未显现)。技术迭代的过程往往涉及更根本层面的改进。

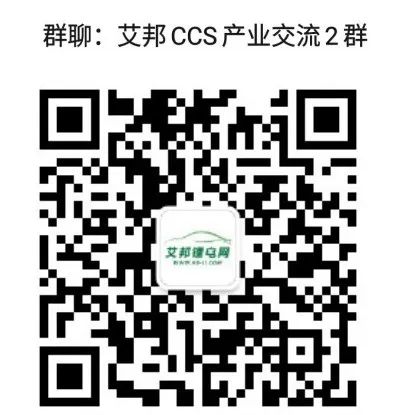
活动推荐:第四届新能源电池CCS集成母排产业论坛(3月20日 苏州)
二、报名方式
艾果儿:183 1256 0351(同微信)
邮箱:ab008@aibang.com
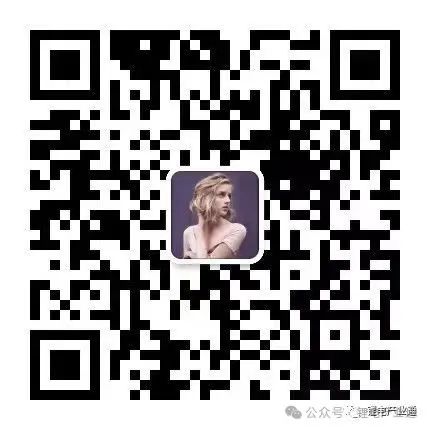
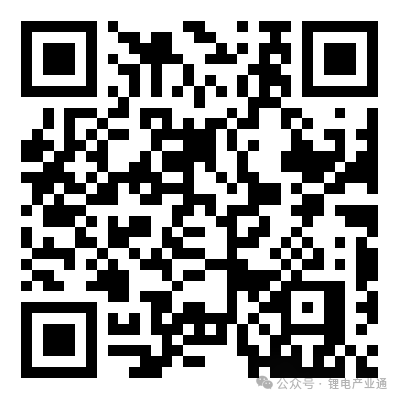
新能源汽车的快速发展带动了动力电池的高速增长。动力电池生产流程一般可以分为前段、中段和后段三个部分。其中,前段工序包括配料、搅拌、涂布、辊压、分切等,中段工序包括卷绕/叠片、封装、烘干、注液、封口、清洗等,后段主要为化成、分容、PACK等。材料方面主要有正负极材料,隔膜,电解液,集流体,电池包相关的结构胶,缓存,阻燃,隔热,外壳结构材料等材料。 为了更好促进行业人士交流,艾邦搭建有锂电池产业链上下游交流平台,覆盖全产业链,从主机厂,到电池包厂商,正负极材料,隔膜,铝塑膜等企业以及各个工艺过程中的设备厂商,欢迎申请加入。
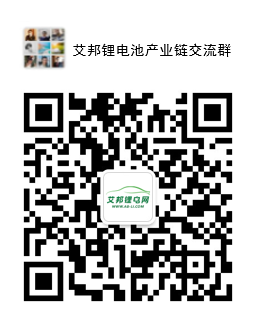
长按识别二维码关注公众号,点击下方菜单栏左侧“微信群”,申请加入群聊