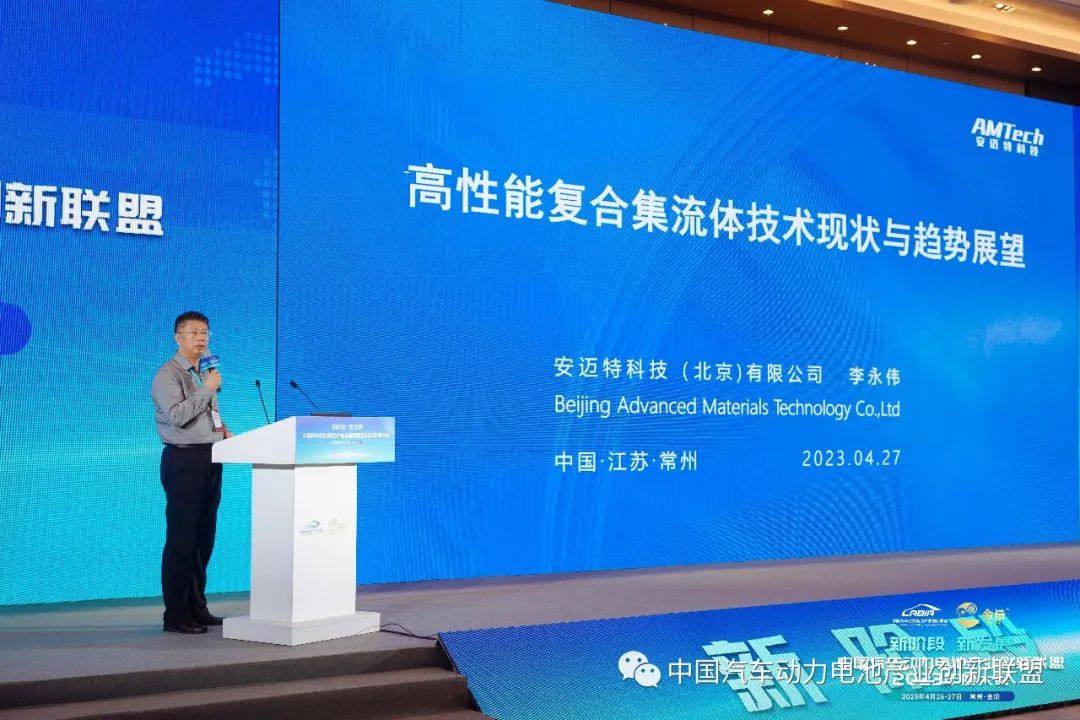
以下内容为现场演讲实录:
各位嘉宾,大家上午好!非常荣幸动力电池创新联盟提供这样的机会,向大家汇报一下最近复合集流体技术和产业发展的新的动态。
电池产业的发展,二十年时间,从几百亿市场已经到上万亿大的市场规模,对各种材料的需求提升速度非常快。
从产业发展来讲,2025年达到1500GWh,2030年达到3000GWh以上,整个市场规模目前能够看出来非常明确的趋势。对应这样的需求,对现在正极集流体、负极集流体需求量也非常大。到2025年,从市场来讲,铝箔市场会达到347亿左右,铜箔市场达到1000亿以上。两个加起来,2030年有可能达到接近3000亿左右的市场,总市场量非常大。
从电池发展来讲,电池能量密度在持续改进和提升,从最开始100Wh/kg电池,到现在可以商业化的已经达到350Wh/kg左右。最近消息,宁德时代的凝聚态电池提出来能量密度是500Wh/kg。最新报道,电池能量密度已经可以提升到700Wh/kg。这样更高能量密度对电池的安全性要求越来越高。
从电池热失控过程来讲,如果能够在最早期切断热失控发生和扩展,对于电池的安全性可以提供根本的保障。
复合集流体这样一个新的技术来提供一个主动安全的保障。我们碰到比较多的是机械滥用、电滥用和热滥用,最终可能都体现在电池热失控方面,导致电池燃烧、爆炸问题。同时电池在发展过程里,对成本、对续航里程方面也提出了更高的要求。
复合集流体从结构上来讲,之前大家听到的铜箔、铝箔都是纯金属的箔材,现在的复合集流体可以采用类似于三明治的结构,中间的基体类似于PET,而上下两个面上通过各种制备技术,能够提供微米级的导电层。
从电池特性来讲,并不是说一定要用那么厚的铜箔、铝箔,集流体主要有两个功能:一是能承载活性材料,一是提供导电能力。
从安全性来讲,复合集流体这一超薄的金属层、导电层的结构,在毫秒级时间里能够熔断。因为电池短路和正常使用的电流应该会有十几位到几十位电流的差异,这个差异足以让导电层在毫米时间熔断。
复合集流体具备几个方面优势:
1.高安全性。
2.降成本,尤其对复合铜箔来讲,减少了60%-70%铜的使用。铜的使用跟整体成本相比,相对现在铜箔成本降低20%-30%。
3.高能量密度,现在铝箔主流厚度在12微米左右,如果采用复合铝箔可以轻松把它的厚度降低6-8微米,在体积能量密度上有贡献。
4.重量,铜的比重是8.96,PET比重是1.3左右,按照6微米左右的复合铜箔,整体比重是在3.89左右,对电池能量密度提供5%-6%的贡献。
5.使用量,对有色金属行业就是比较显著的贡献,按照2030年3000GWh用铜材的使用,大概这个使用量应该是在160万吨左右,如果少2/3可以减少100万吨的使用,对电池行业绿色制造也是比较大的贡献。
6.工艺适应性,它的导电层非常薄,只有1微米左右,不会出现平常讲到比较多的电池热失控里出现毛刺问题、出现金属异物问题,这些特性都是相比于现在铜箔、铝箔所体现出来的比较优势。
复合集流体这种产品的概念出现比较早,最早可以追溯到1992、1993年,2011年5月帝人杜邦薄膜在“人与车科技展2011”上 将PEN薄膜“Teonex”用于锂离子充电电池集电体;2020年10月份,斯坦福崔屹团队也展出了他们基于PI-TPP-金属复合集流体,超轻、自熄,具有更好的安全特性。2021年7月OPPO闪充开放日上发布“夹心式安全电池”,为五层安全结构的“三明治” 集流体代替铝箔集流体。宁德时代新能源公司多功能复合集流体技术获得2021年世界新能源技术创新奖。
比较典型的复合集流体与传统铜箔/铝箔结构。减重幅度,复合铜箔可以减重56%,电芯减重可以贡献4.5%,能量密度可以提升5.6%左右。对正极来讲,因为厚度进一步减薄,对减重幅度贡献会更大一些。
从基膜上来讲,基膜提供了整个复合集流体的关键支撑,PET、PP,基于原材料和制成,目前相对比较成熟;PI具备更好的性能,但是目前成本比较高,而且现在比较难做到更薄;PET和PP基本上可以达到2-3微米,最薄可以做到这样的程度,这为更好、更高性能的复合集流体也提供了很好的支撑。
跟传统铝箔相比,复合铝箔和传统铝箔工艺,相对来讲传统铝箔制造工艺比较长,这里既有前端的精炼的过程,然后铸轧,通过铸轧再做成薄板,薄板再精轧成我们所需要的现在主流的12-15微米的厚度。而现在复合铝箔制造工艺相对比较简单,基本在一台设备上就可以完成这样的功能。
如图,主要通过真空环境里蒸镀工艺直接收卷,在一台设备上很短流程就可以完成,而且环境、能耗和制造过程的控制可以达到更精密的程度。
对铜箔来讲,大家比较熟悉的是几个主要工艺,主要包括溶铜的工艺、生箔工序、后处理、保护,以及分切工序。这里核心的是生箔工序。
目前在复合集流体方面还没有整体完成大规模制造的工艺,而现在的工艺主要有两大类:湿法工艺和干法工艺。湿法工艺有两步法:磁控溅射+水电镀,这是大家听到比较多在做的。基于磁控溅射+水电镀工艺里为了提高整线效率,也有一些公司开发了磁控溅射+蒸镀+水电镀,为什么加蒸镀,核心主要是为后面的水电镀提供一个更高的导电能力电极,让整体速度能够提升起来。也有公司在开发化学镀的方法。
干法工艺采用超薄金属箔材进行贴合的工艺。真空沉积是安迈特科技主要在做的,复合铜箔就要采用磁控溅射+真空蒸镀的办法,能够一步形成1000纳米或1微米厚度的沉积能力。基于这一比较,目前像复合铝箔上大家都是采用真空蒸镀,行业里现在普遍需要蒸镀24左右才能够形成1000纳米的厚度。通过真空沉积技术的突破,能够一次形成1000纳米,同时材料性能上与它们相比有比较突出的优势,能够整体提升20%左右。
复合铜箔,我们开发了基于全真空干法的工艺,这对于工艺生产来讲占地面积、成本相比于现在湿法工艺都有比较突出的优势。基于目前我们正在推动的2亿平方米的产业化项目,做测算,在整个项目投资上会比它们降低20%~30%。
这几个指标是目前复合集流体的关键指标:
方阻,也就是导电能力,基于一次蒸镀和多次蒸镀,能够控制它的方阻在35毫欧以下,多次蒸镀目前在40毫欧左右。实际在做的时候,典型值可能是在31-32左右。
结合力是复合集流体的关键指标,因为我们要解决金属层和基膜层结合,这个结合在电池制造过程里,比如涂布、滚压、极片成型,包括在电解液的浸泡和后面循环过程中都要满足电池整体要求。结合力提升重点是要通过材料的改性、界面的设计,以及加工工艺优化来实现。
抗拉强度、延展力这些指标是主要面向现在超薄和极薄的复合集流体的发展趋势。比如复合铜箔跟现在4.5微米的铜箔相比,在这样的强度下能够提供一个更高的强度和延展性,更好了能够适用于极片超薄化的发展。
表面张力可以通过调控。如图,通过多次蒸镀和一次蒸镀得到材料金属层结构,一次成膜,是完整的晶体结构,多层结构,多层对导电能力来讲还是有比较大的影响。目前正在量产推动的复合铝箔情况,这个产品已经进入到可以批量生产的程度。我们正在中试开发的复合铜箔的情况,这个材料预计在年中6、7月份能完成中试。
复合集流体在导入电池里并不是对现有生产工艺完全没有影响,因为它的结构上并不是纯金属,在后面的电池组装过程里需要有一个滚焊工艺把它的极耳部分连接起来,行业的发展已经推动到可以采用超声滚焊的方式,制造速度可以达到60-80米的焊接速度,完全可以跟现在规模制造速度匹配。实际焊接效果从目前我们得到的用户反馈来讲,比照现在常规的金属箔材内阻增加,做得好大概百分之十几,甚至可以接近现在电池内阻情况。
把这个材料进行了动力电池里应用验证,跟我们合作伙伴在110Ah,能量密度360Wh/kg中导入进去,比较好地能通过针刺和挤压的测试,已经得到了验证。目前推进,在动力电池里,客户已经开始在批量导入。
从整体行业发展来讲,这样的技术追溯到1992、1993年,真正开始启动是在2017年前后才推动起来。从全球来看,在这个行业发展方向上,中国应该是居于最前列的。日本爱发科目做设备的,TDK是做材料的,东丽是做基膜的,松下也在推动这方面工作;在美国,主要是美国的应用材料以及Sorteria公司在推动这方面工作;在欧洲,主要是以德国公司为主,包括冯-阿登纳、Fraunhofer、莱宝光学、BOBST等公司;在中国已经形成了初步的产业规模,可能这两天在苏州也有同样一个复合集流体行业会议,这已经是行业里第三次会议了。这里集聚了比较多的进入到这个行业里的传统集流体企业、基膜材料企业、做钯材的企业、做装备的企业,包括一部分头部电池企业,初创公司目前有30多家公司在推进相关工作。如图,在国内这些都是已经开始在推动复合集流体产业化的公司。除了这些公司之外,后面支撑的还有很多做装备、做原材料的公司也在推动,应该在很快时间里可以形成规模制造的产业支撑。
从总体发展来讲,目前已经完成了第一阶段产品验证的工作,第二阶段从今年开始到明年是这个产品方向一个很重要的发展节点,对于头部电池企业会加快推进这个产品的导入,对复合集流体产业方面,包括装备企业,会比较快地推动规模量产的工作,不断去提高产品性能,降低成本。第三阶段在大规模量产预计在2024、2025年形成产业快速发展阶段。
从发展来讲,在2030年左右,预计大概能够形成接近2000亿左右的市场。如果能把它的导电能力进一步提升的话,有70%-80%以上的市场空间可以替代。
从下一步发展来讲,相信复合集流体只是我们在推进电池技术进步里的一个起点。
未来电池发展会更多去实现集成制造,进一步降低电池制造环节,进一步降低成本。在复合集流体上还有很多工作,作为新的技术导入进来之后,还有很大的发展空间,对高能量密度,复合集流体可以通过材料设计的轻型化,包括固态电池内串结构集成,以及安全特性提升高能量密度,也就是说如果导入复合集流体,对于未来300Wh/kg、400Wh/kg、500Wh/kg继续往下走,能够提供一个更好的安全性支撑。
在快速充电方面,我们也正在开发三维结构复合导电结构来提升导电性能。
在长寿命方面,因为它可以对电极膨胀有更好的容纳性,也对电池的循环寿命有比较大的提升。
在低成本方面,从目前装备行业支撑来讲,可以做成集成制造,把多个单工序、分立的工序变成集成制造的工序,也可以节约更多金属铜使用。现在看到是替代2/3的铜,未来可能能够替代铜的比例会进一步提升。
从安全方面来讲,从半导体行业里借鉴更多技术集成,可以实现从本质安全到智能安全的改进和提升,实现早期感知预警,比如一些PTC技术,可以跟电极更好地集成起来。
从电池产业发展来看,我们借鉴比较多的卷对卷的技术,这些技术从半导体行业借鉴。从电池产业发展来看,目前电极制造、电池组装还是在毫秒级、亚毫秒级层面上,半导体行业很多技术的开发是在纳米层级去做的,我们也希望找到一条新的路,在纳米级和毫米级技术中间,在微米级加工精度上,既能实现高精度制造,同时也能够实现大规模制造和低成本结合,我们在这里推动这项工作。
不管是动力电池还是材料,还是制造和服务,未来相信都是对几个关键指标:安全性、性能、循环寿命、功率特性、能量密度、环境适应性、机电可靠性等指标,不管对动力电池、储能电池还是其他电池来讲,核心一点都是能量转换效率以及对储能付出的成本到底到什么程度。
技术发展是加速非常快的,从产品技术开发到转向市场化,应该成为我们主要去推动的因素。所以我们也提出SPECt发展驱动的模式来推动我们产品的开发。
我们公司成立时间很短,2021年底刚刚成立,我们集成了这个行业里优秀的人才,包括国际上比较大的先进的装备企业跟我们共同合作。在国内我们也有很多合作伙伴,因为我们团队对电池制造、电池设计以及电池材料有比较多的积累,把这些优势比较快地集成到这个项目上,能快速去推进。
目前我们已经开始启动2亿平方米的制造,预计到2024年6月份可以全面投产,希望我们的团队对复合集流体的发展、对于动力电池和电池产业整体的发展能够做出我们的贡献。
谢谢大家!
新能源汽车的快速发展带动了动力电池的高速增长。动力电池生产流程一般可以分为前段、中段和后段三个部分。其中,前段工序包括配料、搅拌、涂布、辊压、分切等,中段工序包括卷绕/叠片、封装、烘干、注液、封口、清洗等,后段主要为化成、分容、PACK等。材料方面主要有正负极材料,隔膜,电解液,集流体,电池包相关的结构胶,缓存,阻燃,隔热,外壳结构材料等材料。 为了更好促进行业人士交流,艾邦搭建有锂电池产业链上下游交流平台,覆盖全产业链,从主机厂,到电池包厂商,正负极材料,隔膜,铝塑膜等企业以及各个工艺过程中的设备厂商,欢迎申请加入。
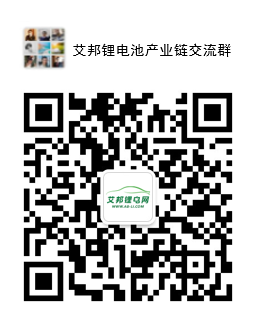
长按识别二维码关注公众号,点击下方菜单栏左侧“微信群”,申请加入群聊