- What is a Cell Contact System
CCS( cell contact system) is a critical component at the heart of the battery pack, playing a vital role in ensuring the battery's reliable performance and longevity. CCS consists of signal acquisition components (options: wire cable, PCB, FPC, FFC, etc.), plastic structural parts(options:PET film,blister tray, plastic bracket, etc.), busbars, which are combined together through methods like hot pressing or hot riveting. This setup enables serial and parallel connections between battery cells, and the collection and transmission of signals such as temperature and voltage. It is a part of the BMS (Battery Management System) and is widely used in fields such as new energy vehicles and electrochemical energy storage (EES).
△ The application of CCS in electric vehicle battery packs, image source: Audi
The hot riveting process starts with preparing raw materials such as thermoformed trays or injection-molded brackets, signal collection components (FPC/PCB/FFC, etc.), and aluminum busbars. First, electrical connections between the nickel tabs and aluminum busbars are made through welding. Then, the signal collection components are fixed onto the brackets using hot riveting. After this, the assembly undergoes visual inspection and electrical performance testing before being packaged and stored in inventory.
△ Process Flow Chart,image source:Shenzhen Yilian Technology Co., Ltd.
The hot pressing process involves assembling raw materials such as signal collection components (FPC/PCB/FFC, etc.), aluminum busbars, and PET insulation films. These are then placed in the working area of a hot press. By applying specific temperatures and pressures, the aluminum busbars and signal collection components are pressed together into a thin sheet. Subsequently, electrical connections between the nickel tabs and aluminum busbars are established through welding. The assembly then undergoes visual inspection and electrical performance testing before being packaged and stored in inventory.Thermal lamination is for cell contact systems using insulation films.
△ Process Flow Chart,image source:Suzhou West Deane New Power Electric Co.,Ltd (WDI)
The key equipment in the above two processes are the hot pressing machine and the hot riveting machine. So, who supplies these devices? Let me introduce the equipment suppliers for CATL, the world's largest battery manufacturer.
-
XINDINGYUAN AUTOMATIC
XINDINGYUAN AUTOMATIC established in 2010, is a manufacturer specializing in the research and development of precision thermal control press-fit equipment and intelligent control. The company focuses on providing customers with automated solutions for hot pressing, thermal melting, hot riveting, and ultrasonic equipment.
The company offers professional CCS thermal forming equipment for customers: PET insulation film hot press assembly and PC thermoformed hot riveting assembly equipment, which include features such as automatic aluminum loading, ultrasonic FPC welding, laser nickel sheet welding applications, AOI inspection, electrical performance testing, CCS hot press fully automatic lines, and injection molding/thermoforming hot riveting automatic lines.
CCS industry-related customers include CATL, Uniconn, Ningde Kaili, YNTECH , Amphenol, AKM Meadville, Dongguan Silicon , MGE, Vivtoury, HMEV, HT-Group, and more than 30 other enterprises. The related equipment automatic lines have cumulatively delivered more than 100 sets and have been successfully put into production.
-
Product
-
Hot press prototyping and small batch trial production CCS pressing equipment
-
Hot Press Mass Production Model—Single Layer Automatic Line for CCS assembly
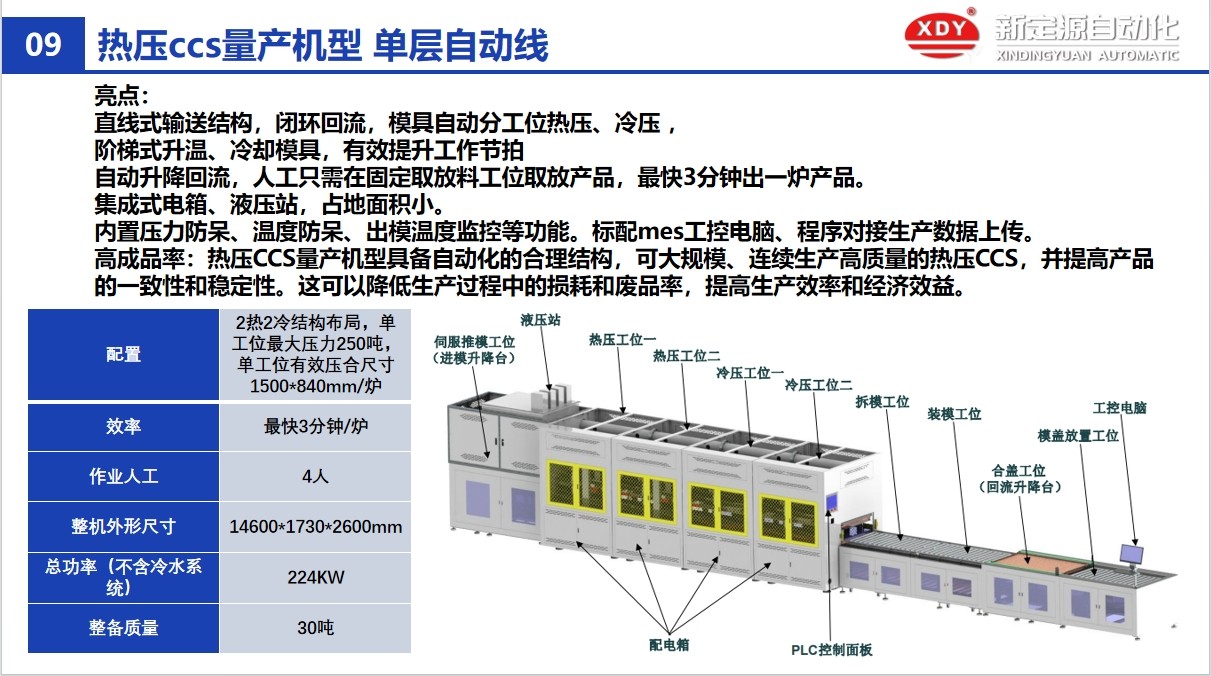
-
Hot Press Mass Production Model—Multi-layer Hot Press Automatic Line for CCS assembly
-
Hot Riveting Equipment for CCS Prototyping
-
Hot Riveting Flexible Mass Production Single Machine for CCS assembly
-
Hot Riveting Large-Scale Continuous Production Equipment for CCS assembly
If you need to place an order, please contact us directly at
E-mail:001@aibang.com
TEL : 18666186648