在电动汽车动力总成中,电池 (CCS) 发挥着重要作用:它们确保可靠且可监控的电池运行,并通过互连电池实现电池的双向电流流动。德国和欧洲的汽车行业现已在 CCS 生产方面积累了丰富的知识。
德国知名理工学府,也是世界顶尖的理工科大学之一的德国亚琛工业大学“电动汽车部件生产工程 (PEM)”主席委托德国 Manz 公司进行的市场研究,显示了 CCS (cell contacting systems) 的趋势和市场未来几年技术变革对CCS生产所带来的重大影响。借助 Manz 的自动化生产解决方案,汽车制造商和供应商已做好迎接挑战的准备。
欧洲的电动汽车电池生产正在加速 - 随之而来的是对电池(CCS) 的需求。凭借其生产设备,德国Manz AG 多年来一直支持知名汽车制造商和供应商进行电动传动系统部件的全自动化生产。因此,在 CCS 的生产中,机器制造商的工艺知识和生产专业知识也相应较高。
市场目前非常活跃,对 CCS 制造商的要求将从根本上改变。在 Manz 委托的独家市场研究中,亚琛工业大学“电动汽车部件生产工程 (PEM)”主席研究了 CCS 的主要发展。由此可以推导出以下趋势:
趋势 1:新的、改进的电池系统架构
过去,电池单体、电池模块和电池包三个层次的电池系统结构是常见的,但这种结构越来越多地被明确界限所取代。趋势是所谓的 Cell-to-X (CTX) 电池系统。
电池到电池组 (Cell-to-Pack):与其他概念相比,CTP 概念具有一些优势,例如更高的能量密度、更容易制造、更好的散热和更高的刚性。
电池到底盘 ( Cell-to-Chassis):电池单元直接内置于车辆底部,电池组与底盘融合在一起。与CTP相比,CTC不仅减轻了重量,还实现了更好的散热和更高的刚性,有助于提高安全性和更好的车辆控制。
模块到底盘(Module-to-Chassis):此处完全组装的电池模块内置于车辆底部。MTC 概念提供了许多优势,例如更大的设计灵活性和更易于维护,因为可以更轻松地更换有缺陷的模块。
趋势 2:电池的能量含量更高
对于圆柱形、棱柱形电池和软包电池,将会发生影响 CCS 架构的变化。
圆柱形电池:标准直径从之前的 21 毫米增加到 46 毫米,因此体积和能量含量增加了五倍。
棱柱形电池:平均能量含量翻倍,从目前的 100 Ah 增加到 200 Ah 以上。
软包电池:能量含量也显着增加——但这种增加更难以量化。
CCS 的结果:组件变得越来越大,集成度越来越高,以便尽可能减少工作步骤,从而降低模块组装成本。未来的 CCS 将从目前最长边缘处的不到 50 厘米增长到有时高达 200 厘米!
趋势三:完全预组装的CCS
未来,汽车制造商将期望供应商尽可能多地进行 CCS 预组装,以尽可能降低电池模组和系统生产的下游成本。平均而言,每辆车必须制造七个CCS,最多包含 30个单独的零件。机器和设备制造商必须提供适当的设备概念,以便通过高度预组装以低成本和可靠的方式制造大量单个组件。
趋势 4:通过本地生产缩短供应链
在查看生产结构时,今天已经很明显,汽车制造商希望电池单元、模块和电池的运输路线尽可能短。未来,大多数汽车制造商将依靠本地生产和本地安装这些电池单元,从而缩短供应电池单元生产、相关电池模块和电池组生产与供应车辆工厂之间的距离。由于 CCS 生产的高度自动化,人员成本在选址决策中起次要作用。对于 CCS 生产,有利的供应链和生产条件、熟练工人的可用性以及机械和设备工程中完整的服务网络等位置因素脱颖而出。
趋势五:标准化程度低
在未来几年,CCS 仍将是一种标准化程度较低的产品,并且在个别汽车制造商和电池格式之间具有很大的差异化潜力。因此,市场上不会集中于少数几个CCS 制造商,而是 CCS 制造商的多元化,针对电池单元格式和系统设计的不同要求进行专业化。因此,在竞争中,尽早为特定系统设计提供满足汽车制造商成本和质量要求的产品和生产概念至关重要。同时,需要一定的灵活性,以根据需要响应设计变更。
趋势 6:过渡到 800V 电池系统
在电池系统中,趋势是朝着 800V 或更高范围内的更高电压发展。从高端汽车开始,800V电池系统也将逐渐在面向大众市场的汽车中站稳脚跟。然而,由于更高的电压而增加的电流对电连接器(母线)的材料、几何形状、连接和热设计提出了更高的要求。最重要的是,在设计 CCS 时,关于增加爬电距离的要求是有问题的。由于电压更高,电弧可能会在更长的距离内产生。CCS 制造商可以通过智能生产概念在这里区分。
新能源汽车的快速发展带动了动力电池的高速增长。动力电池生产流程一般可以分为前段、中段和后段三个部分。其中,前段工序包括配料、搅拌、涂布、辊压、分切等,中段工序包括卷绕/叠片、封装、烘干、注液、封口、清洗等,后段主要为化成、分容、PACK等。材料方面主要有正负极材料,隔膜,电解液,集流体,电池包相关的结构胶,缓存,阻燃,隔热,外壳结构材料等材料。 为了更好促进行业人士交流,艾邦搭建有锂电池产业链上下游交流平台,覆盖全产业链,从主机厂,到电池包厂商,正负极材料,隔膜,铝塑膜等企业以及各个工艺过程中的设备厂商,欢迎申请加入。
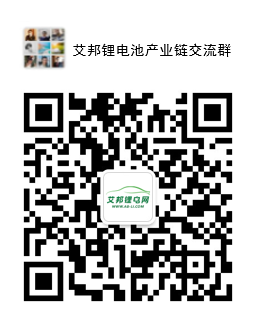
长按识别二维码关注公众号,点击下方菜单栏左侧“微信群”,申请加入群聊