上期,小编给大家详细解读了一个璞泰来复合集流体专利,CN 117254031 A “复合集流体的制备工艺”,这个专利在2023年4月26日申请,2023年12月9日被公开。详情可查看以下链接。
接下来,小编将大家解读另外一个专利,CN 117334920A “一种复合集流体及其制备方法和应用”。这个专利在2023年4月26日申请,2024年1月2日被公开。
这2个专利涉及到的复合集流体制备工艺并不一样,但都采用了涂覆技术。
大家对此内容感兴趣的话,可以关注本公众号,我们会陆续发布复合集流体相关的内容。另外,大家也可以进群参与讨论复合集流体最新工艺,技术。
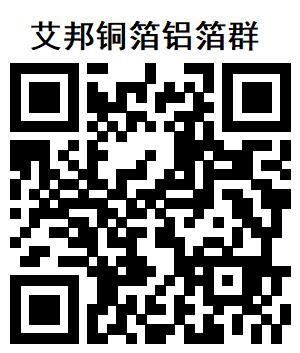
随着新能源汽车技术的不断发展,市场对新能源汽车的需求越来越高,对新能源汽车的性能也提出了更高要求。无论是用于数码产品的锂电池还是电动汽车的电池,都希望电池的能量密度尽量高,电池的重量越来越轻。
如何提升电池的能量密度和安全性,是名大新能源企业急需解决的关键问题。集流体是新能源电池的重要组成部分,通过降低集流体的厚度和重量可以减少电池的体积和重量。目前,铜箔的最小厚度约为6微米,铝箔的最小厚度约为8微米。
复合集流体是由高分子薄膜和金属镀层组合得到,复合集流体大致可以分为复合铜和复合铝箔。
目前复合铜箔成品多应用于电池负极。大部分复合铜箔都是采用蒸发镀+水电镀的方式生产,蒸发镀的效率低、镀层薄,同时水电镀的阴极长铜速率低、能耗大、宽幅窄等一系列因素,导致用这种方法生产出的复合铜箔存在成本高昂,生产效率低,针孔多等缺陷,在一定程度上也限制了复合铜的大面积推广与使用。
(1)将现有的铜箔粘接在基材上。这种方法对粘结剂的粘接力没有特殊的要求,能将铜箔粘在基材上即可,复合铜箔的厚度难以进一步缩小,铜表面平整光滑。
(2)直接在基材上形成铜镀层。形成铜镀层的方法主要有电镀、化学气相沉积(CVD)、物理气相沉积(PVD)等,这几种方法对基材要求较高,或者需要在基材表面设置保护层,或者需要基材的材质和/或厚度能够承受反应条件(通常是高温)的冲击。
此外,现有技术生产的金属层厚度均一性不易做选择性控制,比如过于光滑的外表面会导致正极活性材料的附着力不足,在后道的正极制备工艺中,又需要针对界面增加工序和处理成本;集流体作为锂离子电芯内电路的重要环节,上述过于均一的厚度和材质,也不便于做更多熔断安全设计。
本发明提供一种复合集流体及其制备方法和应用,旨在显著提高复合集流体工作过程的安全性。复合集流体,包括绝缘层,绝缘层具有相对设置的两个端面,在至少一个端面上设置有粘接层和金属箔层,且粘接层位于绝缘层和金属箔层之间。
1.在绝缘薄膜层上涂覆粘结剂得到过渡件,利用电沉积的方法在阴极装置上形成铜箔。
聚合物薄膜可选聚对苯二甲酸乙二醇酯、聚酰胺、聚酰亚胺和聚丙烯等。
粘结剂为热固胶,粘结剂包括至少一种线性聚合物和至少一种交联聚合物,线性聚合物包括环氧树脂、丙烯酸树脂和聚苯醚,交联聚合物包括酚醛树脂、聚氨酯、双马来酰亚胺、马来酸酐、交联聚丙烯和交联聚乙烯;
线性聚合物与交联聚合物的质量比为1:15-35;优选为1:25。粘结剂的初始粘连力为1N-10N。为保证产品的耐腐蚀性,聚合物粘结剂需耐电解液腐蚀,聚合物粘结剂在85℃环境下,在含有1000ppm水的电解液中浸泡120h后,膨胀率小于4%。
电沉积所采用的电镀液中,金属盐离子的浓度为0.5mol/L-2mol/L,氢离子的浓度为1.0mol/L-3.0mo1/L,氯离子的浓度为50ppm/L-200ppm/L;阴极装置的线速为1m/min-15m/min,电流密度为20-50A/dm2; 极装置的形状为环带状或圆辊状,材质选自钛、镍、铝、不锈钢、锆和铬中的至少一种,阴极装置的表面粗糙度Ra值为0.1-0.5。
在绝缘层上涂覆粘结剂的过程可以采用涂布工艺,如微凹涂布、狭缝涂布、网纹涂布、刮刀涂布或辊涂布中的至少一种。
2.将过渡件从复合压辊和阴极装置之间穿过,待阴极装置上沉积得到金属箔层之后,施加压力通过复合压辊将阴极装置表面的金属箔层,通过粘结剂粘接至过渡件上,然后经过抗氧化处理和熟化处理之后得到单面复合集流体产品。
抗氧化处理是将膜卷置于抗氧化液中,浸泡5s-15s,抗氧化液的组成不限,可以为葡萄糖+六价铬溶液或无铬钝化液。
3.利用单面复合集流体产品,在绝缘层的另一端面上重复上述制备过程,得到双面的复合集流体。
本发明采用的先电沉积再转移涂覆贴合的工艺,制备的复合集流体具有以下优势:
1.通过设计具有绝缘层、粘接层和金属层的集流体结构,控制金属箔层的厚度小于等于3.5um,使金属箔层远离粘接层的一侧端面维持一定的粗糙度Ra,同时使金属箔层的强度小于金属箔层与粘接层界面的结合力。这样,在遭受巨大外力冲击下,产生较大形变时,金属箔层易于沿平面断裂,既能够切断内电路又不会对结构上产生附带的威胁,针对特定的场景提升安全性。
2.使电镀工艺和设备大大减化,与传统的直接蒸发镀+电镀的工艺而言,该工艺设备投入低,生产速率和良率均有显著提升。
3.在蒸发+水电镀的传统复合铜箔工艺中,因蒸发镀和水电镀的工艺限制,复合铜箔中的导电层导电能力较差,会导致复合集流体的金属层厚度不均匀,电导率低,内阻大等一系列不良影响。本发明中工艺依托阴极装置沉积金属,在低电流密度下,仍能生产出致密的金属箔膜,表面光洁平整,无针孔铜箔。
4.本发明中的复合集流体宽幅由阴极装置的宽幅而决定,生产效率较现行同厚度锂电复合集流体大幅度提升。
为了更清楚地说明本发明的技术方案,下面列举一个制备复合铜箔的实例介绍。
(1)绝缘层选用厚度为3um的PP膜,走膜速度为10m/min,采用微凹涂布的方式,粘结剂为聚丙烯和环氧树脂,其中聚丙烯的分子量控制在20万以下,聚丙烯和环氧树脂的比例为50:1,将粘结剂涂布到绝缘层表面得到过渡件,粘结剂厚度为0.5um,将带有粘结剂的PP膜覆上离型膜,防止卷面互相粘结导致绝缘层破损。
(2)金属辊选用钛辊,粗糙度Ra为0.3,电镀液的铜离子浓度为1.5mo1/L、氢离子浓度为1mo1/L、氯离子浓度为100ppm/L、电流密度为25A/dm2。
(3)将步骤(1)得到的过渡件去除离型膜,再将过渡件从复合压辊和阴极装置之间穿过。
(4)完成穿带后开启电沉积装置,待钛辊表面生长出致密的铜层后,将带有粘结剂的PP膜通过压辊,将钛辊上的铜层粘连到PP膜上。钛辊的线速度为5m/min,得到的铜箔厚度为1.5um。
(5)抗氧化液为8g/L葡萄糖+0.5g/L六价铬的混合溶液,随后,带铜箔的PP膜在抗氧化液中浸泡5s后,最后将带铜箔的PP膜表面的水分烘干后即得到复合铜箔的单面半成品,然后进行熟化。
(6)待胶水熟化后,在半成品复合铜箔另一侧再次进行涂布粘结剂,依次进行铜箔剥离复合、抗氧化、熟化后,即可得到完整的复合铜箔产品。
经检测:得到的复合铜箔在含1000ppm水的电解液中浸泡120h没有发生脱落
为了更好促进行业人士交流,艾邦搭建有锂电池铜箔铝箔微信群,包括铜箔,铝箔,原材料等材料企业以及铜箔铝箔生产过程中的设备厂商,欢迎大家申请加入。
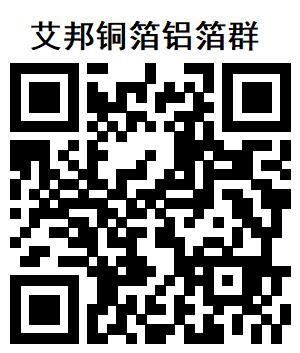
新能源汽车的快速发展带动了动力电池的高速增长。动力电池生产流程一般可以分为前段、中段和后段三个部分。其中,前段工序包括配料、搅拌、涂布、辊压、分切等,中段工序包括卷绕/叠片、封装、烘干、注液、封口、清洗等,后段主要为化成、分容、PACK等。材料方面主要有正负极材料,隔膜,电解液,集流体,电池包相关的结构胶,缓存,阻燃,隔热,外壳结构材料等材料。
为了更好促进行业人士交流,艾邦搭建有锂电池产业链上下游交流平台,覆盖全产业链,从主机厂,到电池包厂商,正负极材料,隔膜,铝塑膜等企业以及各个工艺过程中的设备厂商,欢迎申请加入。
长按识别二维码关注公众号,点击下方菜单栏左侧“微信群”,申请加入群聊